Производство автоклавного газобетона – это точная технология, где каждый компонент играет критическую роль. Неправильный подбор или пропорции ведут к браку, перерасходу сырья, снижению прочности и ухудшению теплоизоляции. Методика подбора – это не просто рецепт, а системный подход, основанный на свойствах сырья и требуемых характеристиках конечного продукта (плотность, прочность, морозостойкость).
Основная часть
Определение целевых параметров автоклавного газобетонного блока:
Плотность (D): Основополагающий параметр (D300, D400, D500 и т.д.). Определяет теплопроводность и прочность. Чем ниже плотность, тем выше требования к точности подбора и качеству сырья.
Прочность на сжатие (Класс B): Требуется для несущих способностей (B1.5, B2.0, B2.5 и т.д.).
Морозостойкость (F): Важно для наружных стен (F25, F35, F50, F100).
Требования к геометрии: Влияет на выбор ПАВ и режимов вспучивания/твердения.
Прочность на сжатие (Класс B): Требуется для несущих способностей (B1.5, B2.0, B2.5 и т.д.).
Морозостойкость (F): Важно для наружных стен (F25, F35, F50, F100).
Требования к геометрии: Влияет на выбор ПАВ и режимов вспучивания/твердения.
Анализ и подготовка сырья для газобетона:
Песок (кремнеземистый компонент):
Требования: Модуль крупности (оптимально 1.5-2.0), чистота (содержание глинистых, илистых частиц, органики – должно быть минимально, нормируется ГОСТ), влажность (постоянная или учет при дозировании).
Подготовка: Мокрый или сухой помол до удельной поверхности 280-450 м²/кг (Blaine). Тонкость помола напрямую влияет на скорость реакции с известью и конечную прочность.
Известь (Кальциевая составляющая):
Требования: Активность (CaO+MgO акт. - минимум 70%, оптимально >85%), скорость гашения (оптимально – средняя или быстрая, 5-15 мин), температура гашения (контроль перегрева смеси), негабарит (частицы >0.6 мм – минимум).
Важность: Основной участник реакции образования гидросиликатов в автоклаве. Низкая активность или медленное гашение – брак по прочности и трещины.
Цемент (Связующее):
Требования: Марка (обычно ПЦ500 Д0 или Д20), сроки схватывания (нормальные), тонкость помола. Обеспечивает начальную прочность смеси до автоклавирования.
Алюминиевая пудра (Газообразователь):
Требования: Тип (ПАП-1, ПАП-2), активный Al (мин. 82-90%), дисперсность (удельная поверхность). Количество рассчитывается строго исходя из требуемого объема газа (пористости) и активности извести. Переизбыток – большие поры, разрывы, "поседение"; недостаток – недоподъем, высокая плотность.
Вода:
Требования: Чистота, температура (важно для скорости реакции газообразования и схватывания). Водотвердое отношение (В/Т) – ключевой параметр для подвижности смеси и процесса поризации. Оптимальное В/Т обычно 0.55-0.65 и корректируется под конкретное сырье.
Добавки (При необходимости):
Ускорители твердения (CaCl₂, сульфаты – осторожно!).
Пластификаторы/суперпластификаторы (для улучшения удобоукладываемости, снижения В/Т).
Модификаторы структуры (для управления формой и размером пор).
Армирующие волокна (полипропилен).
Требования: Модуль крупности (оптимально 1.5-2.0), чистота (содержание глинистых, илистых частиц, органики – должно быть минимально, нормируется ГОСТ), влажность (постоянная или учет при дозировании).
Подготовка: Мокрый или сухой помол до удельной поверхности 280-450 м²/кг (Blaine). Тонкость помола напрямую влияет на скорость реакции с известью и конечную прочность.
Известь (Кальциевая составляющая):
Требования: Активность (CaO+MgO акт. - минимум 70%, оптимально >85%), скорость гашения (оптимально – средняя или быстрая, 5-15 мин), температура гашения (контроль перегрева смеси), негабарит (частицы >0.6 мм – минимум).
Важность: Основной участник реакции образования гидросиликатов в автоклаве. Низкая активность или медленное гашение – брак по прочности и трещины.
Цемент (Связующее):
Требования: Марка (обычно ПЦ500 Д0 или Д20), сроки схватывания (нормальные), тонкость помола. Обеспечивает начальную прочность смеси до автоклавирования.
Алюминиевая пудра (Газообразователь):
Требования: Тип (ПАП-1, ПАП-2), активный Al (мин. 82-90%), дисперсность (удельная поверхность). Количество рассчитывается строго исходя из требуемого объема газа (пористости) и активности извести. Переизбыток – большие поры, разрывы, "поседение"; недостаток – недоподъем, высокая плотность.
Вода:
Требования: Чистота, температура (важно для скорости реакции газообразования и схватывания). Водотвердое отношение (В/Т) – ключевой параметр для подвижности смеси и процесса поризации. Оптимальное В/Т обычно 0.55-0.65 и корректируется под конкретное сырье.
Добавки (При необходимости):
Ускорители твердения (CaCl₂, сульфаты – осторожно!).
Пластификаторы/суперпластификаторы (для улучшения удобоукладываемости, снижения В/Т).
Модификаторы структуры (для управления формой и размером пор).
Армирующие волокна (полипропилен).
Методика расчета состава (Принципы) газобетона:
Основа: Материальный баланс с учетом требуемой плотности сухого газобетона.
Ключевые соотношения:
Известь: Песок (мольное соотношение CaO : SiO₂): Оптимально ~0.8-1.0 для образования тоберморита. Рассчитывается по активному CaO в извести и содержанию SiO₂ в песке после помола.
Цемент: Обычно 10-20% от массы вяжущего (известь+цемент). Повышает начальную прочность.
Алюминиевая пудра (ПАП): Расчет ведется по формуле, связывающей требуемый объем газа, активность извести и содержание активного Al в пудре. Стартовая точка: ~400-800 г/м³ смеси, корректируется по факту.
Вода (В/Т): Определяется экспериментально для достижения требуемой подвижности смеси (обычно по расплыву конуса 16-22 см). Зависит от тонкости помола песка, активности извести, вида цемента, наличия ПАВ.
Ключевые соотношения:
Известь: Песок (мольное соотношение CaO : SiO₂): Оптимально ~0.8-1.0 для образования тоберморита. Рассчитывается по активному CaO в извести и содержанию SiO₂ в песке после помола.
Цемент: Обычно 10-20% от массы вяжущего (известь+цемент). Повышает начальную прочность.
Алюминиевая пудра (ПАП): Расчет ведется по формуле, связывающей требуемый объем газа, активность извести и содержание активного Al в пудре. Стартовая точка: ~400-800 г/м³ смеси, корректируется по факту.
Вода (В/Т): Определяется экспериментально для достижения требуемой подвижности смеси (обычно по расплыву конуса 16-22 см). Зависит от тонкости помола песка, активности извести, вида цемента, наличия ПАВ.
Лабораторные испытания и оптимизация газобетон:
Пробные замесы: Обязательный этап! Готовятся небольшие партии по рассчитанному составу.
Контроль параметров смеси: Время начала и конца газовыделения, температура, подвижность.
Контроль сырца: Высота подъема, структура пор (визуально), начальная прочность.
Автоклавирование проб: По стандартному режиму (температура, давление, время).
Испытание образцов: Плотность, прочность на сжатие, отпускная влажность, морозостойкость (после циклирования), усадка при высыхании.
Корректировка состава: На основе результатов испытаний вносятся изменения:
Изменение тонкости помола песка.
Корректировка соотношения известь/песок.
Изменение количества цемента.
Точная настройка дозы ПАП.
Оптимизация В/Т.
Введение/корректировка добавок.
Требуется получить автоклавный газобетон средней плотности 500 кг/м3 по литьевой технологии с применением смешанного цементно-известкового вяжущего с возможно большей прочностью.
Объем одного замеса – 10 л.
Исходные материалы: портландцемент ПЦ500–Д0, молотая известь – кипелка активностью 70 %, быстрогасящаяся, кремнеземистый компонент - зола–унос (р = 2,06 г/см3), ПАВ - мылонафт, замедлитель скорости гидратации извести-кипелки - молотый гипсовый камень.
1. Пользуясь соответствующими формулами, подсчитывают расход материалов на один замес с учетом следующих исходных величин:
n = 0,45 (по табл. 1), С = 1,5 (по табл. 2), Kс = 1,1.
По табл. 1. определяют, что расплыв растворной смеси (исходная текучесть) должен быть 30 см при литьевой технологии изготовления ячеистого бетона. Опытным путем устанавливают, что такая текучесть растворной смеси имеет место при В/Т = 0,44.
По табл. 2 находят, что при применении данных материалов удельный объем сухой смеси W = 0,48 л/кг. Коэффициент выхода пор Kп = 1390 л/кг, коэффициент использования газообразователя α = 0,85.
Установив эти величины, производят расчет расхода материалов на один замес:
Вяжущее
Рвяж = 0,5 • 10 / 1,1(1 + 1,5) = 1,8 кг;
известь
Pи = 1,8 • 0,45 = 0,81 кг;
цемент
Pц = 1,8 - 0,81 = 0,99 кг;
кремнеземистый компонент
Pк = 1,8 • 1,5 = 2,7 кг;
молотый гипсовый камень
Рr = 0,81 • 0,03 = 0,024 кг;
вода
B = (1,8 + 2,7) 0,44 = 1,98 л.
Пористость, которую необходимо создать при помощи порообразователя для получения средней плотности,
Пr = 1 - 0,5(0,48 + 0,64) / 1,1 = 0,49 (49 %).
Зная пористость, определяют расход:
алюминиевой пудры
Pп = 0,49 • 10 / 1,39 • 0,85 = 4,15 г;
мылонафта для приготовления водно-алюминиевой суспензии
Pм = 4,15 • 0,05 = 0,21 г.
Хотя в настоящее время современное технологическое оборудование в состоянии обеспечить необходимую точность дозирования компонентов, однако это не всегда гарантирует стабильность получения ячеистобетонной смеси и ячеистого бетона с требуемыми характеристиками. Для каждого вида изделий разрабатываются свои алгоритмы подбора и коррекции состава ячеистобетонной смеси, которые должны обеспечить стабилизацию прочностных свойств, подвижности смеси, степень ее поризации и оптимизацию состава. На современном уровне развития технологии ячеистых бетонов, а также аппаратных средств контроля качества материалов и управления технологическим процессом следует ограничиться только коррекцией состава бетона, которую можно производить двумя принципиально разными методами. Первый состоит в полном расчете состава ячеистого бетона по характеристикам материалов, проводимом как бы «на чистом месте». Второй метод состоит в коррекции заданного лабораторией номинального (базового) состава. В ряде случаев при таком подходе достаточно, не меняя заданного базового состава, скорректировать только фактические расходы материалов для «возврата» к номинальному составу, При этом учитываются факторы наиболее значимые для качества продукции.
Контроль параметров смеси: Время начала и конца газовыделения, температура, подвижность.
Контроль сырца: Высота подъема, структура пор (визуально), начальная прочность.
Автоклавирование проб: По стандартному режиму (температура, давление, время).
Испытание образцов: Плотность, прочность на сжатие, отпускная влажность, морозостойкость (после циклирования), усадка при высыхании.
Корректировка состава: На основе результатов испытаний вносятся изменения:
Изменение тонкости помола песка.
Корректировка соотношения известь/песок.
Изменение количества цемента.
Точная настройка дозы ПАП.
Оптимизация В/Т.
Введение/корректировка добавок.
Требуется получить автоклавный газобетон средней плотности 500 кг/м3 по литьевой технологии с применением смешанного цементно-известкового вяжущего с возможно большей прочностью.
Объем одного замеса – 10 л.
Исходные материалы: портландцемент ПЦ500–Д0, молотая известь – кипелка активностью 70 %, быстрогасящаяся, кремнеземистый компонент - зола–унос (р = 2,06 г/см3), ПАВ - мылонафт, замедлитель скорости гидратации извести-кипелки - молотый гипсовый камень.
1. Пользуясь соответствующими формулами, подсчитывают расход материалов на один замес с учетом следующих исходных величин:
n = 0,45 (по табл. 1), С = 1,5 (по табл. 2), Kс = 1,1.
По табл. 1. определяют, что расплыв растворной смеси (исходная текучесть) должен быть 30 см при литьевой технологии изготовления ячеистого бетона. Опытным путем устанавливают, что такая текучесть растворной смеси имеет место при В/Т = 0,44.
По табл. 2 находят, что при применении данных материалов удельный объем сухой смеси W = 0,48 л/кг. Коэффициент выхода пор Kп = 1390 л/кг, коэффициент использования газообразователя α = 0,85.
Установив эти величины, производят расчет расхода материалов на один замес:
Вяжущее
Рвяж = 0,5 • 10 / 1,1(1 + 1,5) = 1,8 кг;
известь
Pи = 1,8 • 0,45 = 0,81 кг;
цемент
Pц = 1,8 - 0,81 = 0,99 кг;
кремнеземистый компонент
Pк = 1,8 • 1,5 = 2,7 кг;
молотый гипсовый камень
Рr = 0,81 • 0,03 = 0,024 кг;
вода
B = (1,8 + 2,7) 0,44 = 1,98 л.
Пористость, которую необходимо создать при помощи порообразователя для получения средней плотности,
Пr = 1 - 0,5(0,48 + 0,64) / 1,1 = 0,49 (49 %).
Зная пористость, определяют расход:
алюминиевой пудры
Pп = 0,49 • 10 / 1,39 • 0,85 = 4,15 г;
мылонафта для приготовления водно-алюминиевой суспензии
Pм = 4,15 • 0,05 = 0,21 г.
Хотя в настоящее время современное технологическое оборудование в состоянии обеспечить необходимую точность дозирования компонентов, однако это не всегда гарантирует стабильность получения ячеистобетонной смеси и ячеистого бетона с требуемыми характеристиками. Для каждого вида изделий разрабатываются свои алгоритмы подбора и коррекции состава ячеистобетонной смеси, которые должны обеспечить стабилизацию прочностных свойств, подвижности смеси, степень ее поризации и оптимизацию состава. На современном уровне развития технологии ячеистых бетонов, а также аппаратных средств контроля качества материалов и управления технологическим процессом следует ограничиться только коррекцией состава бетона, которую можно производить двумя принципиально разными методами. Первый состоит в полном расчете состава ячеистого бетона по характеристикам материалов, проводимом как бы «на чистом месте». Второй метод состоит в коррекции заданного лабораторией номинального (базового) состава. В ряде случаев при таком подходе достаточно, не меняя заданного базового состава, скорректировать только фактические расходы материалов для «возврата» к номинальному составу, При этом учитываются факторы наиболее значимые для качества продукции.
Таблица №1 Исходное В/Т, обеспечивающее текучесть смеси в соответствии с таблицей №1, устанавливают экспериментально или принимают при литьевой технологии В/Т = 0,35–0,6; при вибрационной технологии В/Т уменьшают на 20–25%
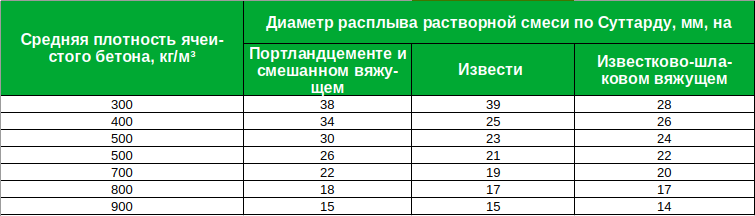
Таблица №2 Для теоретического расчета пористости ячеистого бетона, которая должна создаваться порообразователем, необходимо по таблице №2 принять значение удельного объема сухой смеси Wc.
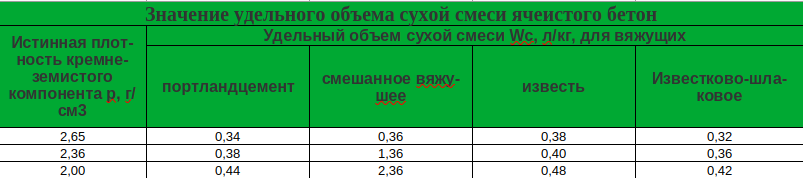
Заключение:
Методика подбора компонентов автоклавного газобетона – это итеративный процесс, требующий глубокого понимания химии и физики процесса, тщательного анализа сырья и проведения серии лабораторных испытаний. Не существует универсальной "идеальной" рецептуры – она всегда адаптируется под конкретное сырье и параметры оборудования. Инвестиции в грамотный подбор и постоянный контроль компонентов окупаются стабильно высоким качеством продукции, минимизацией брака и снижением себестоимости блоков. Регулярный входной контроль сырья и корректировка рецептуры – залог успешного производства.
Нужна консультация по подбору сырья или оптимизации состава для вашего производства? Столкнулись с проблемами качества? Обращайтесь к специалистам Нашей Компании! Мы поставляем не только надежное оборудование для газобетона, но и предоставляем комплексное технологическое сопровождение. Изучайте другие материалы нашего блога «Ячеистый бетон all inclusive+» для углубления знаний!
Методика подбора компонентов автоклавного газобетона – это итеративный процесс, требующий глубокого понимания химии и физики процесса, тщательного анализа сырья и проведения серии лабораторных испытаний. Не существует универсальной "идеальной" рецептуры – она всегда адаптируется под конкретное сырье и параметры оборудования. Инвестиции в грамотный подбор и постоянный контроль компонентов окупаются стабильно высоким качеством продукции, минимизацией брака и снижением себестоимости блоков. Регулярный входной контроль сырья и корректировка рецептуры – залог успешного производства.
Нужна консультация по подбору сырья или оптимизации состава для вашего производства? Столкнулись с проблемами качества? Обращайтесь к специалистам Нашей Компании! Мы поставляем не только надежное оборудование для газобетона, но и предоставляем комплексное технологическое сопровождение. Изучайте другие материалы нашего блога «Ячеистый бетон all inclusive+» для углубления знаний!