Производство автоклавного газобетона (АГБ) – это высокотехнологичный, многостадийный процесс, требующий точного соблюдения рецептур и параметров на каждом этапе. Условно его можно разделить на несколько ключевых блоков:
Подготовка сырьевых материалов для изготовления автоклавного газобетона:
Песок: Основной компонент. Требуется кварцевый песок с минимальным содержанием глинистых примесей и органики. Песок подвергается мокрому или сухому помолу в шаровых мельницах до тонкости помола, обеспечивающей требуемую прочность и скорость реакции.
Вяжущие: Портландцемент (обычно М400Д0 или М500Д0) и молотая известь-кипелка (CaO) высокой активности. Известь должна быть тонкого помола.
Вода: Техническая вода, очищенная от масел и примесей, способных повлиять на процесс газообразования и твердения.
Газообразователь: Чаще всего – алюминиевая пудра (паста) марок ПАП-1 или ПАП-2. При взаимодействии с известью в щелочной среде выделяет водород, создающий поры.
Добавки (при необходимости): Могут использоваться пластификаторы, ускорители твердения, армирующие волокна.
Вяжущие: Портландцемент (обычно М400Д0 или М500Д0) и молотая известь-кипелка (CaO) высокой активности. Известь должна быть тонкого помола.
Вода: Техническая вода, очищенная от масел и примесей, способных повлиять на процесс газообразования и твердения.
Газообразователь: Чаще всего – алюминиевая пудра (паста) марок ПАП-1 или ПАП-2. При взаимодействии с известью в щелочной среде выделяет водород, создающий поры.
Добавки (при необходимости): Могут использоваться пластификаторы, ускорители твердения, армирующие волокна.
Дозирование и приготовление шлама/смеси автоклавного газобетона:
Компоненты дозируются с высокой точностью (допустимые отклонения обычно ±1%) с помощью весовых дозаторов.
Вариант А (Мокрый помол + смешивание): Песок и вода подаются в шаровую мельницу мокрого помола для совместного помола, образуя песчаный шлам. Затем шлам, поступает в шламбассейне (усреднение шлама) для постоянного перемешивания. Далее шлам подается в дозатор и скоростной смеситель.
Вариант Б (Сухой помол + смешивание): Песок и известь подаются в шаровую мельницу сухого помола для совместного помола, образуя известково-песчаное вяжущее. Затем сухой помол и вода, поступает в шламбассейне (гомогенизация) для постоянного перемешивания. Далее шлам подается в дозатор и скоростной смеситель.
Ключевой этап: В конце цикла смешивания в скоростном смесителе, когда масса уже однородна, вводится алюминиевая пудра/паста. Смешивание с газообразователем длится строго ограниченное время (обычно 15-60 секунд), чтобы предотвратить преждевременное газовыделение в смесителе.
Вариант А (Мокрый помол + смешивание): Песок и вода подаются в шаровую мельницу мокрого помола для совместного помола, образуя песчаный шлам. Затем шлам, поступает в шламбассейне (усреднение шлама) для постоянного перемешивания. Далее шлам подается в дозатор и скоростной смеситель.
Вариант Б (Сухой помол + смешивание): Песок и известь подаются в шаровую мельницу сухого помола для совместного помола, образуя известково-песчаное вяжущее. Затем сухой помол и вода, поступает в шламбассейне (гомогенизация) для постоянного перемешивания. Далее шлам подается в дозатор и скоростной смеситель.
Ключевой этап: В конце цикла смешивания в скоростном смесителе, когда масса уже однородна, вводится алюминиевая пудра/паста. Смешивание с газообразователем длится строго ограниченное время (обычно 15-60 секунд), чтобы предотвратить преждевременное газовыделение в смесителе.
Заливка и формование (газообразование и схватывание):
Готовая смесь быстро (в течение 1-3 минут) разливается в предварительно смазанные формы. Формы заполняются на определенную высоту, учитывая последующее "вспучивание" вибрационными иглы. Сразу после заливки начинается реакция газообразования: алюминий реагирует с гидроксидом кальция (из извести) в щелочной среде: 2Al + 3Ca(OH)2 + 6H2O → 3CaO·Al2O3·6H2O + 3H2↑. Выделяющийся водород вспучивает массу. Формы помещаются в зону предварительной выдержки (камера созревания с температурой 35-45°C и влажностью ~70%). Здесь происходит подъем смеси и начальное схватывание (структурообразование) массива. Длительность: 1.5 – 4 часа (Срок созревания зависит как от параметров сырья, так и от внешних условий). Важен контроль скорости подъема и конечной высоты массива.
Резка сырого массива газобетона:
После достижения необходимой пластической прочности (массив должен держать форму, но еще легко резаться) форма подается на участок резки.
С помощью автоматизированных линий резки (резательный комплекс) разрезает сырой массив:
Разрезается по длине, ширине и высоте на блоки заданных размеров.
Точность резки – критически важный параметр для качества готовых блоков (геометрия, допуски). Используются тонкие струны и системы позиционирования.
С помощью автоматизированных линий резки (резательный комплекс) разрезает сырой массив:
Разрезается по длине, ширине и высоте на блоки заданных размеров.
Точность резки – критически важный параметр для качества готовых блоков (геометрия, допуски). Используются тонкие струны и системы позиционирования.
Автоклавная обработка:
Нарезанные сырые блоки на вагонетках загружаются в автоклав – толстостенный стальной цилиндр с герметичной крышкой.
Обработка происходит насыщенным водяным паром под давлением 170-200°C и давлении 10-12 бар (1,2 МПа) в течение 8-16 часов. Цикл включает:
Предварительный вакуум (опционально, для лучшего проникновения пара).
Подъем давления/температуры (2-4 часа).
Изотермическая выдержка (4-8 часов).
Сброс давления (1.5-3 часа).
"Волшебство" автоклавирования: Под действием высокой температуры и давления в среде насыщенного пара происходят реакции гидротермального синтеза. Основные компоненты (SiO2 из песка и CaO из извести/цемента) образуют прочные и стабильные гидросиликаты кальция (тоберморит, CSH(II)), которые и придают АГБ его уникальные прочностные и долговечные свойства.
Разгрузка, сушка (при необходимости) и упаковка:
После автоклавирования и остывания вагонетки выкатываются из автоклава.
Блоки проходят визуальный контроль и выборочный контроль качества (плотность, прочность на сжатие, геометрия). Если блоки имеют повышенную равновесную влажность, их могут досушивать в специальных камерах до требуемых кондиций (обычно до влажности <30% по массе).
Готовые блоки упаковываются в термоусадочную пленку на поддонах для защиты от влаги и механических повреждений при транспортировке и хранении.
Обработка происходит насыщенным водяным паром под давлением 170-200°C и давлении 10-12 бар (1,2 МПа) в течение 8-16 часов. Цикл включает:
Предварительный вакуум (опционально, для лучшего проникновения пара).
Подъем давления/температуры (2-4 часа).
Изотермическая выдержка (4-8 часов).
Сброс давления (1.5-3 часа).
"Волшебство" автоклавирования: Под действием высокой температуры и давления в среде насыщенного пара происходят реакции гидротермального синтеза. Основные компоненты (SiO2 из песка и CaO из извести/цемента) образуют прочные и стабильные гидросиликаты кальция (тоберморит, CSH(II)), которые и придают АГБ его уникальные прочностные и долговечные свойства.
Разгрузка, сушка (при необходимости) и упаковка:
После автоклавирования и остывания вагонетки выкатываются из автоклава.
Блоки проходят визуальный контроль и выборочный контроль качества (плотность, прочность на сжатие, геометрия). Если блоки имеют повышенную равновесную влажность, их могут досушивать в специальных камерах до требуемых кондиций (обычно до влажности <30% по массе).
Готовые блоки упаковываются в термоусадочную пленку на поддонах для защиты от влаги и механических повреждений при транспортировке и хранении.
Контроль качества автоклавной газобетонной продукции:
Контроль осуществляется на всех этапах: входной контроль сырья, контроль параметров смеси (температура, плотность, подвижность), контроль времени газообразования и подъема, контроль прочности сырца перед резкой, контроль геометрии после резки, обязательный контроль прочности, плотности и влажности готовой продукции по ГОСТ или внутренним ТУ. Используются лабораторные испытания (прессы, весы, сушильные шкафы) и измерительный инструмент (линейки, штангенциркули, угольники).
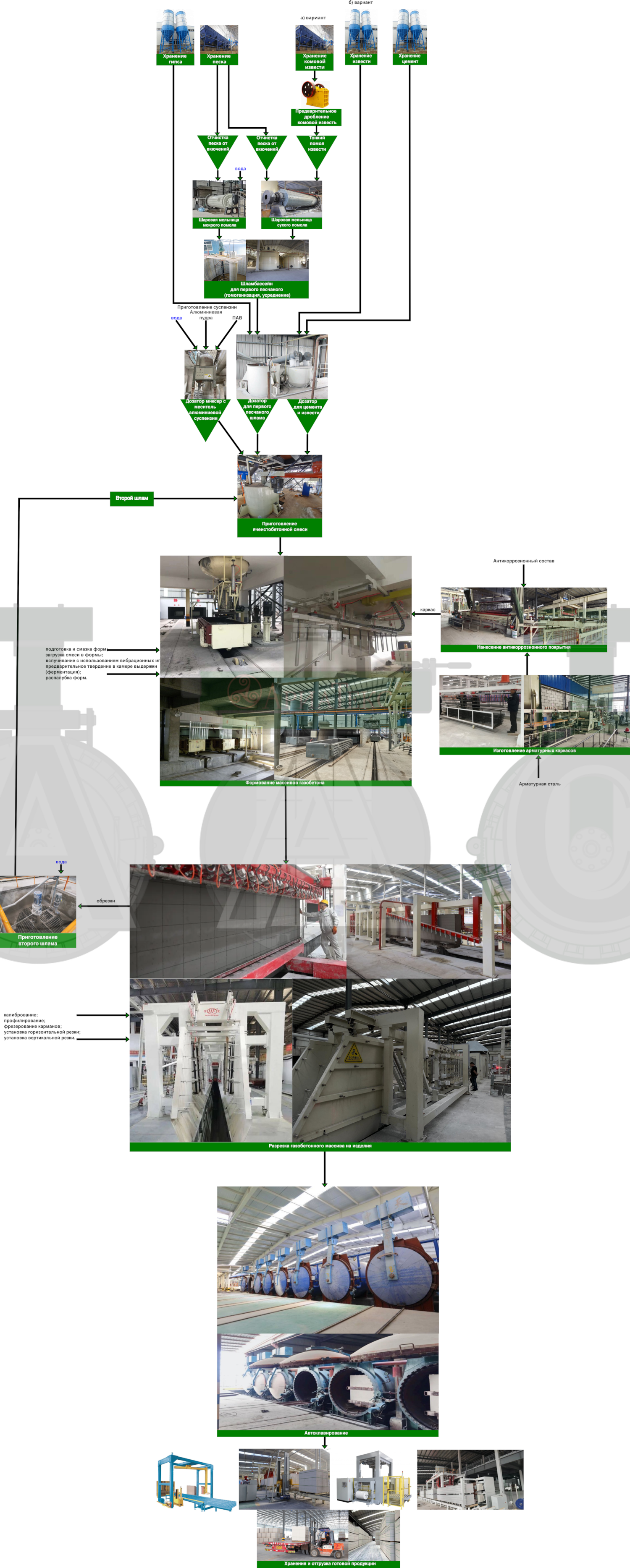
Понимание и точное соблюдение технологической схемы – фундамент успешного производства качественного автоклавного газобетона. Каждый этап, от помола песка до режима автоклавирования, влияет на конечные свойства блоков: прочность, плотность, теплопроводность, точность геометрии и долговечность. Наше оборудование для производства АГБ спроектировано для обеспечения максимальной точности, надежности и эффективности на каждой стадии этого сложного, но удивительного процесса превращения минерального сырья в современный строительный материал.