Рецепт автоклавного газобетона
Измельчение сырьевых компонентов
Измельчение – одна из основных технологических операций, в результате которой достигается не только повышение реакционной поверхности, но и механическое активирование вследствие увеличения свободной энергии. Затрачиваемая энергия расходуется на разрыв химических связей и создание новых поверхностей. При этом изменяется структура твердого тела; появляются дефекты и их скопления; развиваются микро и макротрещины, в результате чего тело разрушается (рис. 1.). При движении трещин в результате необратимых пластических деформаций структура областей, прилегающих к их стенкам, нарушается. Данное явление называют аморфизацией.

Аморфизация кристаллических веществ сопровождается значительным повышением химической активности. К аморфизации склонны кристаллы с большой долей ковалентности химических связей и сложным строением решетки, которое препятствует скольжению плоскостей. К таким веществам относится кварц, корунд, муллит и т.п. С увеличением времени сухого помола измеряемая удельная поверхность порошка не растет, в то время как растворимость в воде непрерывно повышается. Это можно объяснить аморфизацией поверхностных слоев твердых частиц (рис. 2., 3.). Применительно к производству ячеистых силикатных изделий измельчение предусматривает уменьшение диаметра частиц до размеров, сопоставимых с толщиной межпоровых перегородок. Чем ниже плотность ячеистых материалов и соответственно тоньше межпоровые перегородки, тем выше должна быть дисперсность компонентов сырьевой смеси.
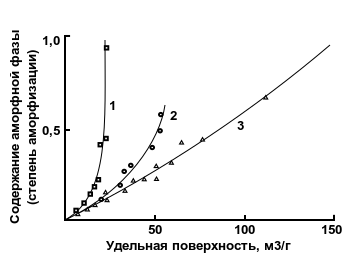
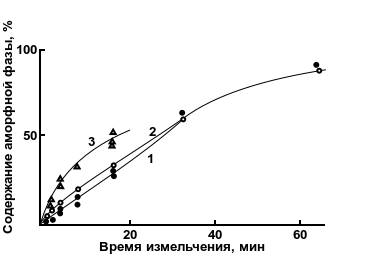
В процессе мокрого помола ярко проявляется эффект П.А. Ребиндера – значительное понижение прочности и твердости измельчаемого материала в результате адсорбции поверхностно-активных веществ. При деформации твердого тела в его поверхностном слое развиваются клиновидные микротрещины, способные смыкаться (залечиваться) после снятия нагрузки. Адсорбированные молекулы, мигрируя по поверхности, достигают устья микротрещин и препятствуют их смыканию. Б.В. Дерягин установил, что пленки жидкости, находящиеся между твердыми поверхностями, оказывают расклинивающее действие, то есть способствуют расширению микрощелей. Кроме того, жидкость эффективно отводит от измельчаемого материала тепло, которое могло бы быть использовано для зарастания микротрещин. Учитывая необходимость получения огромных количеств тонкомолотого кварцевого песка для газосиликата, естественно использование помола в жидкой среде, в частности, в воде. В работах Г.С. Ходакова с сотр. было установлено, что помол кварца с 50-100 % воды от его массы приводит к многократному увеличению его удельной поверхности по сравнению со значениями этой характеристики, полученной помолом в сухом воздухе (табл. 1.). Разница в дисперсности порошков сухого и мокрого измельчения возрастает с увеличением длительности процесса. Применение других жидкостей не приводит к значительному повышению дисперсности частиц.
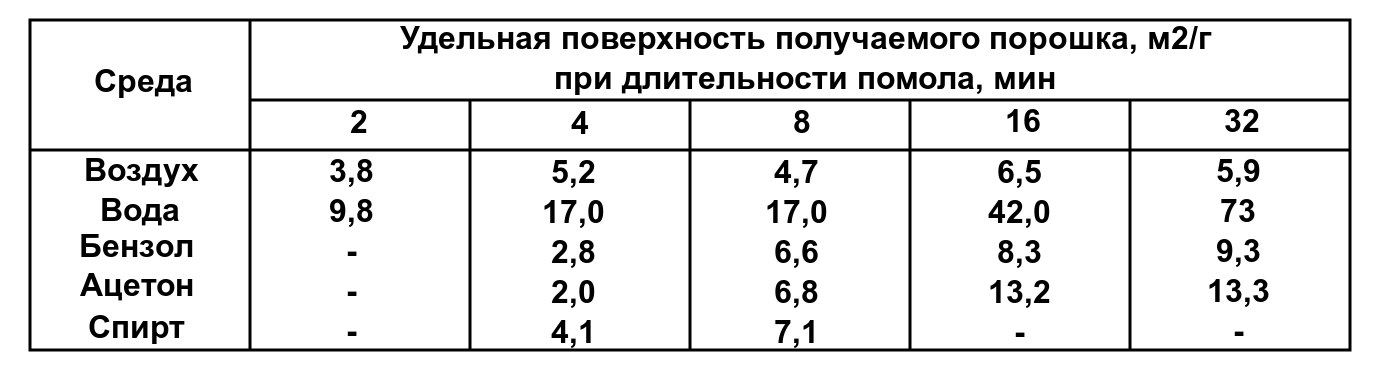
Дальнейшие исследования показали, что многие жидкости оказывают положительное влияние на собственно измельчение (рис. 4.), однако сильный дезагрегирующий эффект проявляется именно в водной среде. Агрегация – образование довольно плотных, но сравнительно малопрочных агрегатов из твердых частиц, пространство между которыми заполнено более мелкими частицами, – искажает результаты измерения дисперсности порошков.
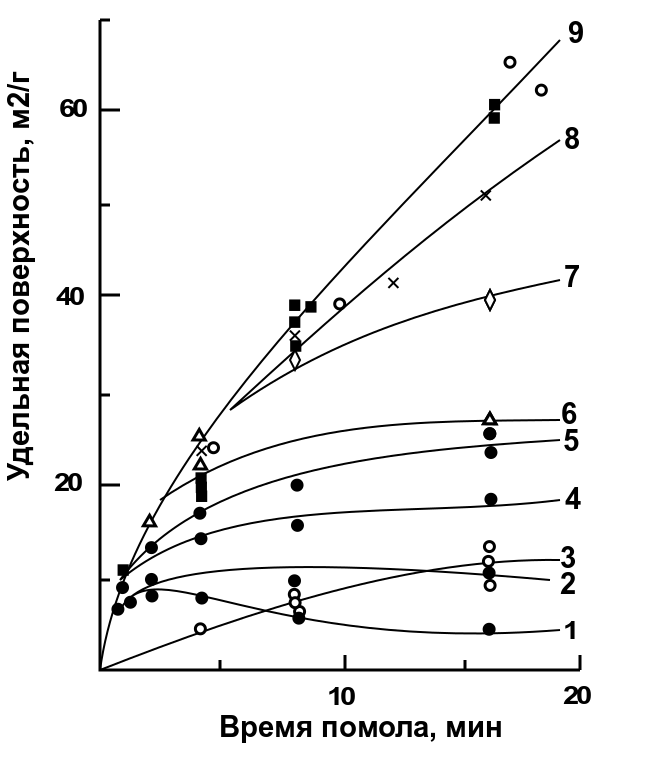
Вода по отношению к кварцу (так же как и по отношению к другим оксидам, силикатам, карбонатам, сульфатам) является одним из самых активных веществ: краевой угол смачивания водой чистой поверхности кварца равен 0 °. В результате даже очень малые добавки воды (~ 0,04 %) сильно влияют на интенсивность измельчения (рис. 5., 6.).
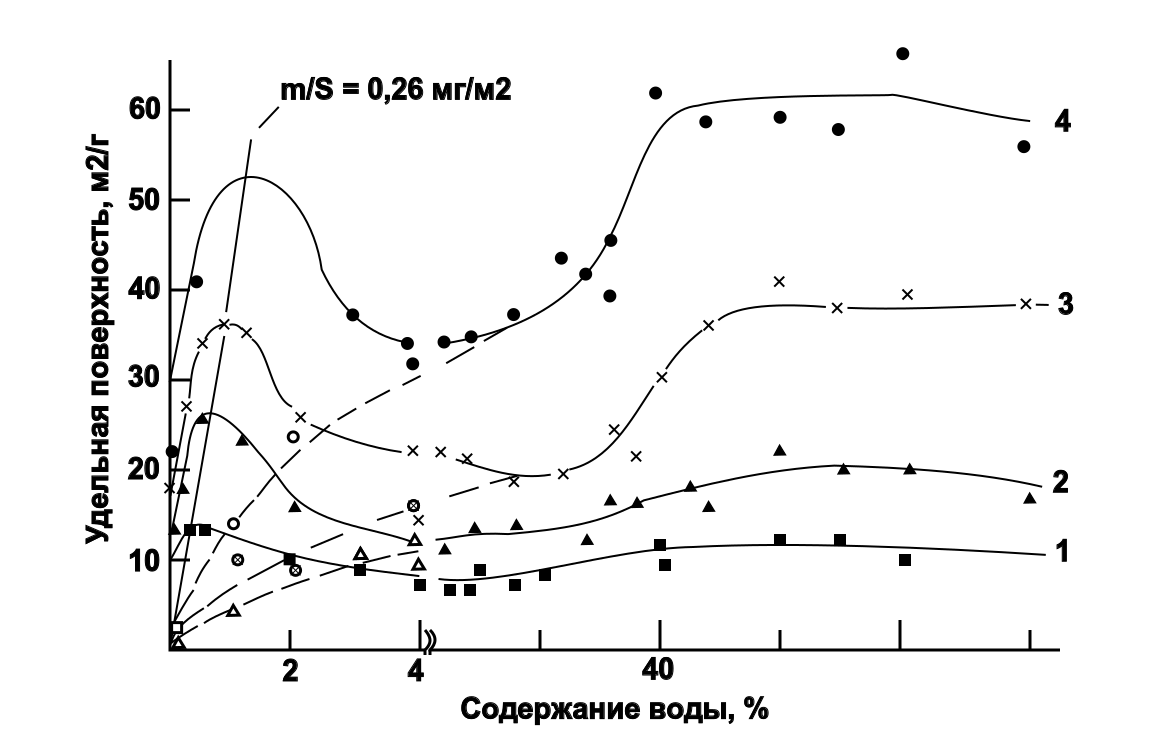
Диспергирование облегчается с увеличением влажности до 1 %, что обусловлено проявлением эффекта Ребиндера. В интервале 1-30 % интенсивность помола значительно снижается из-за образования коагуляционных структур из частиц кварца, соединенных между собой тонкими прослойками воды. Максимумы на кривых (рис. 5..) соответствуют формированию на поверхности порошков (к моменту окончания помола) одного насыщенного мономолекулярного слоя воды. Низкая эффективность измельчения (минимумы на кривых) совпадает с условием наибольшей прочности коагуляционной структуры влажного порошка, при которой средняя толщина оболочек воды вокруг зерен кварца составляет 5-10 насыщенных монослоев. В дальнейшем устойчивость структур падает, так как эффективность действия Ван-дер-Ваальсовых связей распространяется всего на несколько молекулярных радиусов. Последующий рост удельной поверхности обусловливает так называемый мокрый помол. Данный способ измельчения снижает трение между частицами и долю энергии, которая идет на аморфизацию поверхностных слоев. Так, для кварца при сухом помоле средняя толщина аморфизованного слоя составляет ~15 нм, а при мокром – 2 нм. При средней толщине гидратных слоев 40-100 монослоев (0,1-0,02 мкм) содержание воды уже не влияет на измельчение, а значит, повышение влажности до 45 % и выше нецелесообразно.
Аналогичный характер имеют зависимости, характеризующие скорость измельчения кварца (рис. 6.).
Аналогичный характер имеют зависимости, характеризующие скорость измельчения кварца (рис. 6.).
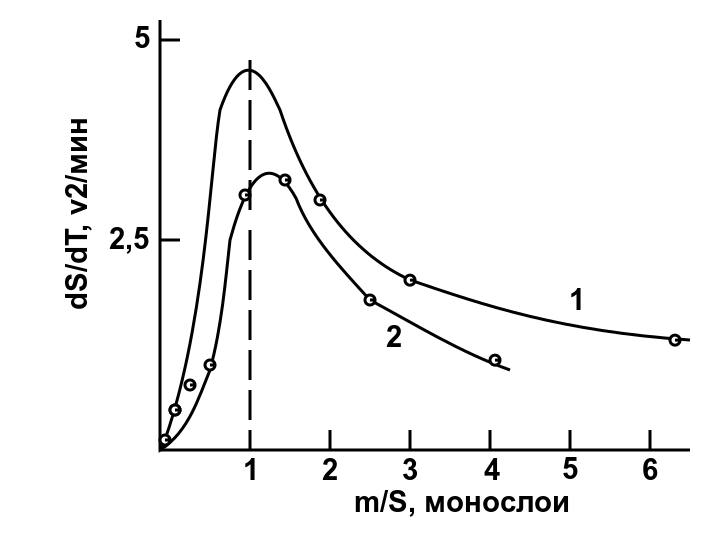
Левые ветви зависимостей обусловлены эффектом облегчения разрушения твердых тел в активной среде (эффектом Ребиндера), тогда как правые ветви отражают образование коагуляционных структур. Действие такой добавки, как триэтаноламин (ТЭА), часто используемой в качестве интенсификатора помола, принципиально не отличается от влияния воды, ацетона, бензола и спирта, взятых в малых количествах (рис. 7.).
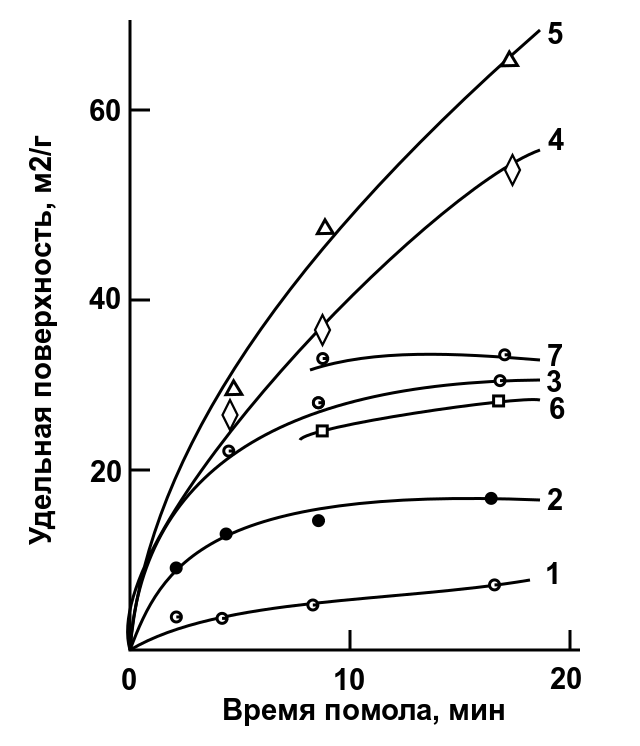
Средние показатели удельной поверхности, м 2 /кг, составляют: для песка в шламе 270, для известково-песчаного вяжущего 485-550; песка в ИПВ 170-190.
Исследование кинетики связывания извести показало, что песок длительного сухого помола является более реакционноспособным по сравнению с песком мокрого измельчения. Известково-песчаное вяжущее получают помолом в шаровой мельнице песка карьерной влажности и извести в соотношении примерно 1 : 1. При совместном измельчении извести и песка под влиянием механических воздействий большой интенсивности происходят механохимические процессы. Это связано с особыми свойствами свежеобразованной поверхности, обладающей высокой химической активностью. Поверхностные слои песчинок аморфизуются, причем степень аморфизации достигает 50 %. Активированные частицы песка в процессе измельчения обволакиваются тонкими слоями извести, что обеспечивает максимально полный контакт между компонентами. В результате не только силикаты, но и низкоосновные гидросиликаты кальция начинают образовываться уже на стадии помола. Потребность в извести при этом снижается. В дальнейшем за счет повышенной растворимости аморфизованного кремнезема формируются множественные устойчивые контакты между кристалликами гидросиликатов кальция, обеспечивающие формирование прочного искусственного камня. За счет влаги песка в процессе помола известь предварительно гидратируется (подгашивается). Регулируя соотношение между песком и известью добиваются оптимальной кинетики гидратации извести и требуемой температуры разогрева ЯБ смеси в период ее вспучивания. При совместном измельчении компонентов одновременно протекает их гомогенизация. При использовании известково-песчаного вяжущего в процессе перемешивания компонентов в смесителе известь равномерно распределяется в смеси, что обеспечивает в конечном итоге высокую гомогенность массы.
Исследование кинетики связывания извести показало, что песок длительного сухого помола является более реакционноспособным по сравнению с песком мокрого измельчения. Известково-песчаное вяжущее получают помолом в шаровой мельнице песка карьерной влажности и извести в соотношении примерно 1 : 1. При совместном измельчении извести и песка под влиянием механических воздействий большой интенсивности происходят механохимические процессы. Это связано с особыми свойствами свежеобразованной поверхности, обладающей высокой химической активностью. Поверхностные слои песчинок аморфизуются, причем степень аморфизации достигает 50 %. Активированные частицы песка в процессе измельчения обволакиваются тонкими слоями извести, что обеспечивает максимально полный контакт между компонентами. В результате не только силикаты, но и низкоосновные гидросиликаты кальция начинают образовываться уже на стадии помола. Потребность в извести при этом снижается. В дальнейшем за счет повышенной растворимости аморфизованного кремнезема формируются множественные устойчивые контакты между кристалликами гидросиликатов кальция, обеспечивающие формирование прочного искусственного камня. За счет влаги песка в процессе помола известь предварительно гидратируется (подгашивается). Регулируя соотношение между песком и известью добиваются оптимальной кинетики гидратации извести и требуемой температуры разогрева ЯБ смеси в период ее вспучивания. При совместном измельчении компонентов одновременно протекает их гомогенизация. При использовании известково-песчаного вяжущего в процессе перемешивания компонентов в смесителе известь равномерно распределяется в смеси, что обеспечивает в конечном итоге высокую гомогенность массы.
Основные закономерности образования рациональной микроструктуры ЯБ
Формирование пористой структуры – один из наиболее ответственных этапов технологического процесса. Под качеством структуры понимают не только средний размер пор и распределение пор по размеру, но и равномерность размещения пор в объеме бетона, отсутствие явных дефектов – расслоений, разрывов межпоровых перегородок, трещин (рис. 8..).
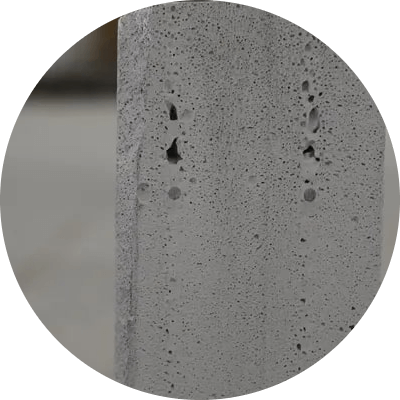
б)
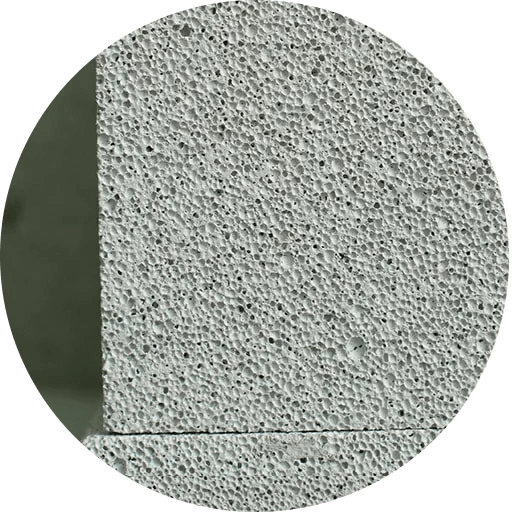
Чем равномернее размещены поры в материале, тем меньше их дисперсия и тем выше прочность ЯБ. Так, изменению дисперсии пористости от 0,05 до 0,01 соответствует повышение прочности на сжатие ЯБ от 2 до 4,5 МПа. Образование качественной структуры на стадии формования, наряду с синтезом низко основных гидросиликатов кальция, способствует повышению коэффициента конструктивного качества (ККК). Пористую макроструктуру можно характеризовать коэффициентом равноосности ячеек, то есть их средней округлостью. Качество ЯБ и изделий из него, в первую очередь, зависит от структуры перегородок между порами и порового пространства (рис. 9.). Структура межпоровых перегородок зависит от минерального состава, степени кристаллизации и дисперсности новообразований. На структуру порового пространства влияет количество и качество макро- и микропор и соотношение между ними.
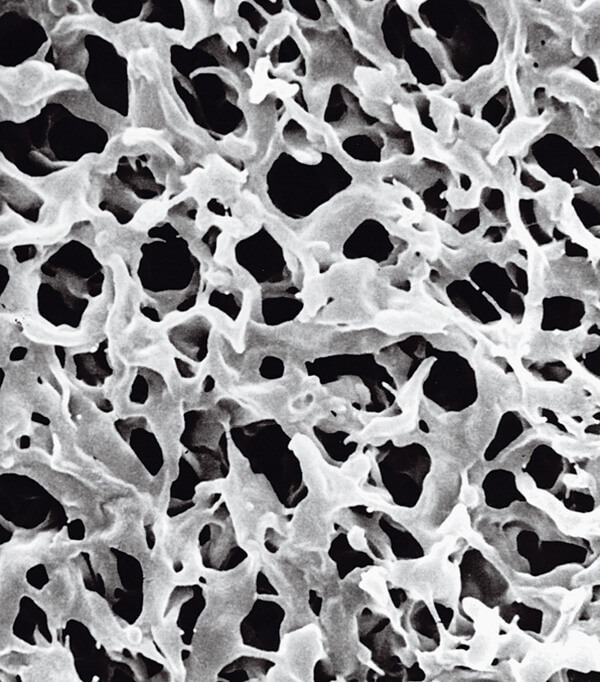
Сущность процесса порообразования при получении газосиликата состоит во взаимодействии алюминия с гидроксидом кальция:
2Аl + 3Са (ОН)2 + 6Н2О = 3СаО∙Аl2О3∙6Н2О+3Н2↑.
Согласно уравнению реакции 1 кг Al выделяет 1,245 м 3 (н.у.) водорода. Реакция идет с достаточной скоростью при температуре 40 °C и выше; ее продолжительность 35-40 мин. На практике потребность в Al больше, так как содержание активного металла в пудре менее 100 %. Кроме того, часть газа теряется во время перемешивания и вспучивания. Это учитывают с помощью коэффициента газо удержания kгу, равного отношению объема Н2, удержанного газобетонной смесью, к теоретически рассчитанному объему газа, выделяемого при данной температуре. Коэффициент газо удержания обычно составляет 0,7-0,85. В соответствии с законом действующих масс количество водорода mH2 , выделяющегося за время τ, можно определить по уравнению:

где gAl – фактор пересчета алюминия на водород, равный 0,1125; mAl – масса алюминия до начала реакции; n – константа скорости химической реакции. Измерив количество водорода, выделяющегося за различные промежутки времени, рассчитывают константу скорости реакции n. Если ее величина превышает 0,05, то такую алюминиевую пудру можно использовать без специальных средств для регулирования газообразования. При n < 0,05 газовыделение замедлено, что отрицательно сказывается на качестве формируемой ячеистой структуры. В этом случае повышают температуру смеси, например за счет увеличения температуры воды затворения, или вводят щелочные добавки для достижения бо́льшей величины рН. Средний размер пор в газобетоне при применении прокаленной пудры 0,5-3 мм; пудра с ПАВ дает поры меньшего размера. Интенсивность реакции газовыделения зависит от дисперсности пудры и чистоты ее поверхности, щелочности и температуры среды, которая должна быть равна 35-45 °C. Для интенсификации процесса газообразования в смесь можно вводить добавки NaOH, тонкомолотого угля, подвергать массу вибрации или использовать другие приемы. Продолжительное газовыделение вызывает либо значительную просадку смеси, либо возникновение усадочных трещин, размеры и количество которых растут с увеличением плотности газобетона. Усадочные трещины могут возникать также при некорректном выборе дисперсности газообразователя.
ГБ смесь представляет собой структурированную вспучивающуюся упруговязкую среду, обладающую тиксотропными свойствами. Реология и плотность массы непрерывно меняются вследствие физико-химических явлений, происходящих в ходе вспучивания и структурообразования. Скорость выделения водорода регулируют так, чтобы она соответствовала скорости нарастания вязкости массы. Газовыделение должно заканчиваться к моменту потери подвижности. Если схватывание опережает газообразование, то смесь затвердевает до того, как завершится выделение водорода. В этом случае межпоровые перегородки окажутся пронизанными трещинами, и требуемая плотность и прочность не будут достигнуты. При замедленном схватывании конечный результат будет тем же, но по другим причинам. Медленное взаимодействие вяжущих с водой приводит к неполной гидратации, то есть возможности вяжущей композиции не используются в полной мере. Схватывание в конце вспучивания массы способствует закреплению полученной структуры. В начале газовыделения пластично-вязкие свойства массы должны нарастать медленно, а в конце – быстро. Для этого используют различные технологические приемы: изменяют температуру формовочной смеси и воды, применяют добавки для регулирования скорости гашения извести и др. Если во время формования вязкость ячеистобетонной смеси ниже оптимальной (высокое отношение В/Т), то масса не в состоянии удержать выделяющийся газ, последний безвозвратно теряется; в результате масса "проседает", ее плотность увеличивается. Завершение газовыделения не совпадает с набором массой требуемой несущей способности (пластической прочности). Если вязкость выше оптимальной, то вспучивание изделий замедляется, и ЯБ массив не достигает заданной высоты. При этом резко увеличивается давление в ячейках, вызывающее появление трещин в межпоровом материале и расслоение в бетоне. Отклонения вязкости смеси от оптимальной в обоих случаях приводят к разрушению микроструктуры и низкому качеству бетона. Предельное напряжение сдвига раствора должно быть меньше внутреннего давления в газовом пузырьке, так как иначе не произойдет равномерного вспучивания массы. Условие невсплывания газовых пузырьков может быть установлено из уравнения Стокса:
ГБ смесь представляет собой структурированную вспучивающуюся упруговязкую среду, обладающую тиксотропными свойствами. Реология и плотность массы непрерывно меняются вследствие физико-химических явлений, происходящих в ходе вспучивания и структурообразования. Скорость выделения водорода регулируют так, чтобы она соответствовала скорости нарастания вязкости массы. Газовыделение должно заканчиваться к моменту потери подвижности. Если схватывание опережает газообразование, то смесь затвердевает до того, как завершится выделение водорода. В этом случае межпоровые перегородки окажутся пронизанными трещинами, и требуемая плотность и прочность не будут достигнуты. При замедленном схватывании конечный результат будет тем же, но по другим причинам. Медленное взаимодействие вяжущих с водой приводит к неполной гидратации, то есть возможности вяжущей композиции не используются в полной мере. Схватывание в конце вспучивания массы способствует закреплению полученной структуры. В начале газовыделения пластично-вязкие свойства массы должны нарастать медленно, а в конце – быстро. Для этого используют различные технологические приемы: изменяют температуру формовочной смеси и воды, применяют добавки для регулирования скорости гашения извести и др. Если во время формования вязкость ячеистобетонной смеси ниже оптимальной (высокое отношение В/Т), то масса не в состоянии удержать выделяющийся газ, последний безвозвратно теряется; в результате масса "проседает", ее плотность увеличивается. Завершение газовыделения не совпадает с набором массой требуемой несущей способности (пластической прочности). Если вязкость выше оптимальной, то вспучивание изделий замедляется, и ЯБ массив не достигает заданной высоты. При этом резко увеличивается давление в ячейках, вызывающее появление трещин в межпоровом материале и расслоение в бетоне. Отклонения вязкости смеси от оптимальной в обоих случаях приводят к разрушению микроструктуры и низкому качеству бетона. Предельное напряжение сдвига раствора должно быть меньше внутреннего давления в газовом пузырьке, так как иначе не произойдет равномерного вспучивания массы. Условие невсплывания газовых пузырьков может быть установлено из уравнения Стокса:
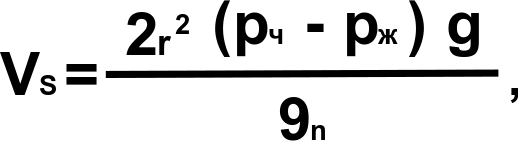
где Vs – установившаяся скорость частицы, м/с; r – радиус Стокса частицы, м; g – ускорение свободного падения, м/с²; ρч – плотность частиц, кг/м³; ρж – плотность жидкости, кг/м³; η – динамическая вязкость жидкости, Па∙с. Частица движется вниз, если ρч > ρж, или вверх при ρч < ρж. Выбрав соответствующее значение скорости всплывания пузырька (например 2∙10 -5 м/с), можно определить необходимое значение вязкости раствора. Для подбора оптимальных условий структурообразования строят кинетические кривые изменения объема массива ΔV и пластической вязкости τ смеси во времени (рис. 10..).
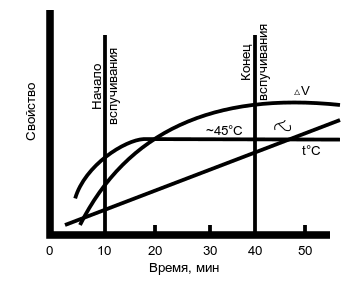
На практике часто ограничиваются определением расплыва массы на вискозиметре Суттарда. К факторам, обусловливающим структуру межпоровых перегородок, относят: вид сырья, состав сырьевой смеси, количество воды затворения, способ формования, наличие химических добавок, условия твердения. На строение межпорового пространства оказывает влияние вид, количество и качество порообразователя, соотношение В/Т, способ формования, ввод добавок. Количество воды затворения непосредственно влияет на число микропор и косвенно – на число макропор и качество макропористой структуры. С увеличением содержания воды затворения (до определенных пределов) в затвердевшем бетоне появляется больше микрокапилляров, уменьшается вязкость смеси, и, следовательно, легче происходит ее вспучивание при введении газообразователя и равномернее распределяются макропоры в объеме бетона Укрупненные поры могут быть вызваны некорректно подобранной вязкостью ячеистобетонной смеси и неподходящим гранулометрическим составом газообразователя. А.А. Федин предложил модель формирования ячеистой пористости, позволяющую проанализировать влияние основных технологических факторов (В/Т, температура смеси) на характер процессов вспучивания и созревания смеси. На схеме (рис. 11..) представлены 9 характерных областей, различающихся условиями формирования ячеистой структуры.
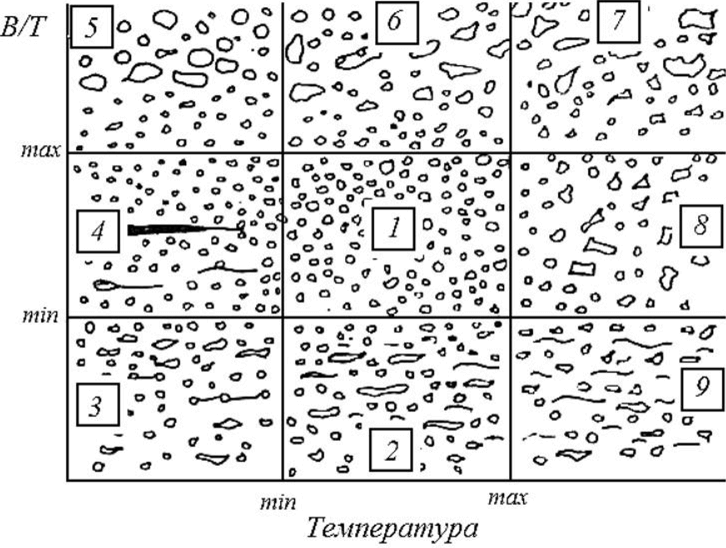
Оптимальной структурой, характеризующейся равномерным распределением мелких пор примерно одинакового размера, является структура 1. При содержании воды, превышающем максимально оптимальное (области 5, 6, 7), наблюдается "ложное кипение". В области 5 процесс вспучивания и схватывания массы идет медленно. Образование ячеистой структуры сопровождается периодами просадки, что определяет крайне неоднородную структуру ячеистого бетона: верхние слои отличаются повышенной прочностью, а плотность средних и нижних слоев в 1,3–1,5 раза выше, чем в верхних слоях.
Для области 7 характерна высокая температура и малая вязкость в первом периоде газообразования. Быстро развивающиеся процессы гидратации влияют на реологию смеси: резко увеличивается вязкость, что в совокупности с большой скоростью газообразования приводит к появлению очень крупных пор неправильной формы в виде многогранных фигур. Характерный внешний признак этой зоны – образование очагов выделения газа наподобие малых гейзеров. Этот процесс длится в течение 2-4 мин, затем наступает полное схватывание. Область 6 характерна для порообразования при малой вязкости. Увеличение вязкости отстает от газообразования, и поэтому давление внутри пузырьков падает; форма пор изменяется, и наблюдается их агрегирование. Внешне можно заметить ложное кипение, которое наступает, однако, значительно раньше, чем в зоне 5. Иногда этот процесс повторяется вновь в конце вспучивания, но уже с просадкой массы. Если содержание воды меньше минимально оптимального, то наблюдается заметное ускорение схватывания, опережающее по скорости газовыделение, продолжающееся и в полусхватившемся материале (области 3, 2, 9). В результате не обеспечиваются нормальные условия вспучивания; структура ухудшается за счет появления сплющенных пор с крупными кавернами, образовавшимися вследствие скопления газа. По мере увеличения температуры (зоны 2 и 9) поры все более заметно вытягиваются в горизонтальном направлении; становятся явно выраженными трещины небольшой (несколько сантиметров) длины, которые также расположены горизонтально. При температуре, близкой к 100 °C, эти трещины встречаются настолько часто, что придают излому панели вид обнаженных сланцевых пород. Причина образования слоистой структуры в этих областях – ранняя (в течение 10-15 мин) потеря подвижности и интенсивное порообразование. В производственной практике распространен такой ход образования ячеистой структуры, когда схватывание и газовыделение полностью совпадают по времени, а затем температура повышается, приближаясь к 100 °C, то есть процесс переходит из области 1 в область 8. Ячейки в таком материале имеют правильную форму, их размеры мало отличаются, однако межпоровые перегородки пронизаны мельчайшими трещинами, образовавшимися за счет интенсивного паровыделения в схватившемся сырце. Причинами такого явления следует считать применение высокоэкзотермической извести с растянутыми сроками гашения, а также перегрев воды в процессе приготовления формовочной массы. Формирование ячеистой структуры с параметрами, характерными для области 4, когда начальное значение вязкости находится в пределах, соответствующих требованиям, а температура ниже 87 °C, происходит при медленном вспучивании без ложного кипения. Образующиеся поры имеют правильную форму и равномерно распределены в объеме материала. Однако в таких изделиях часто встречаются внутренние горизонтальные трещины. Это, повидимому, связано с неравномерными объемными изменениями материала в изделиях, вызванными переходом извести в более стабильное состояние.
Вязкость смеси можно понизить за счет тиксотропного разжижения смеси – разрушения слабых коагуляционных структур и перевода защемленной (иммобилизованной) и частично адсорбированной воды в свободное состояние с помощью динамических воздействий. С этой точки зрения эффективно действие вибрации, улучшающее условия выделения газа. Сочетание вибрации и введения ПАВ приводит к резкому снижению предельного напряжения сдвига ЯБ смеси и в меньшей степени вязкости массы. Эти изменения реологии предотвращают седиментацию грубодисперсных частиц и коалесценцию газовых пузырьков, а значит, позволяют получить мелкопористую ячеистую структуру без дефектов перегородок. При вибрационном способе регулирования пластично-вязких свойств масс оптимальными считают следующие режимы и параметры вибрации: в первый период вспучивания (до достижения максимальной скорости газовыделения) частота вибрации 20-30 с -1 , амплитуда 0,5-0,75 мм; при снижении интенсивности вспучивания характеристики понижаются до 15-20 с -1 и 0,25-0,5 мм соответственно. При скорости вспучивания менее 0,5-1 см/мин вибровоздействие на смесь прекращают. При этом разрушенные структурные связи быстро восстанавливаются, пластическая прочность и несущая способность поризованной массы интенсивно растут. Применение вибрационной технологии позволяет использовать высоковязкие ЯБ массы с низким расходом воды затворения. На рис. 12 приведены результаты исследований по кинетике нарастания пластической прочности массивов, сформированных в различных условиях (табл.2.).
Для области 7 характерна высокая температура и малая вязкость в первом периоде газообразования. Быстро развивающиеся процессы гидратации влияют на реологию смеси: резко увеличивается вязкость, что в совокупности с большой скоростью газообразования приводит к появлению очень крупных пор неправильной формы в виде многогранных фигур. Характерный внешний признак этой зоны – образование очагов выделения газа наподобие малых гейзеров. Этот процесс длится в течение 2-4 мин, затем наступает полное схватывание. Область 6 характерна для порообразования при малой вязкости. Увеличение вязкости отстает от газообразования, и поэтому давление внутри пузырьков падает; форма пор изменяется, и наблюдается их агрегирование. Внешне можно заметить ложное кипение, которое наступает, однако, значительно раньше, чем в зоне 5. Иногда этот процесс повторяется вновь в конце вспучивания, но уже с просадкой массы. Если содержание воды меньше минимально оптимального, то наблюдается заметное ускорение схватывания, опережающее по скорости газовыделение, продолжающееся и в полусхватившемся материале (области 3, 2, 9). В результате не обеспечиваются нормальные условия вспучивания; структура ухудшается за счет появления сплющенных пор с крупными кавернами, образовавшимися вследствие скопления газа. По мере увеличения температуры (зоны 2 и 9) поры все более заметно вытягиваются в горизонтальном направлении; становятся явно выраженными трещины небольшой (несколько сантиметров) длины, которые также расположены горизонтально. При температуре, близкой к 100 °C, эти трещины встречаются настолько часто, что придают излому панели вид обнаженных сланцевых пород. Причина образования слоистой структуры в этих областях – ранняя (в течение 10-15 мин) потеря подвижности и интенсивное порообразование. В производственной практике распространен такой ход образования ячеистой структуры, когда схватывание и газовыделение полностью совпадают по времени, а затем температура повышается, приближаясь к 100 °C, то есть процесс переходит из области 1 в область 8. Ячейки в таком материале имеют правильную форму, их размеры мало отличаются, однако межпоровые перегородки пронизаны мельчайшими трещинами, образовавшимися за счет интенсивного паровыделения в схватившемся сырце. Причинами такого явления следует считать применение высокоэкзотермической извести с растянутыми сроками гашения, а также перегрев воды в процессе приготовления формовочной массы. Формирование ячеистой структуры с параметрами, характерными для области 4, когда начальное значение вязкости находится в пределах, соответствующих требованиям, а температура ниже 87 °C, происходит при медленном вспучивании без ложного кипения. Образующиеся поры имеют правильную форму и равномерно распределены в объеме материала. Однако в таких изделиях часто встречаются внутренние горизонтальные трещины. Это, повидимому, связано с неравномерными объемными изменениями материала в изделиях, вызванными переходом извести в более стабильное состояние.
Вязкость смеси можно понизить за счет тиксотропного разжижения смеси – разрушения слабых коагуляционных структур и перевода защемленной (иммобилизованной) и частично адсорбированной воды в свободное состояние с помощью динамических воздействий. С этой точки зрения эффективно действие вибрации, улучшающее условия выделения газа. Сочетание вибрации и введения ПАВ приводит к резкому снижению предельного напряжения сдвига ЯБ смеси и в меньшей степени вязкости массы. Эти изменения реологии предотвращают седиментацию грубодисперсных частиц и коалесценцию газовых пузырьков, а значит, позволяют получить мелкопористую ячеистую структуру без дефектов перегородок. При вибрационном способе регулирования пластично-вязких свойств масс оптимальными считают следующие режимы и параметры вибрации: в первый период вспучивания (до достижения максимальной скорости газовыделения) частота вибрации 20-30 с -1 , амплитуда 0,5-0,75 мм; при снижении интенсивности вспучивания характеристики понижаются до 15-20 с -1 и 0,25-0,5 мм соответственно. При скорости вспучивания менее 0,5-1 см/мин вибровоздействие на смесь прекращают. При этом разрушенные структурные связи быстро восстанавливаются, пластическая прочность и несущая способность поризованной массы интенсивно растут. Применение вибрационной технологии позволяет использовать высоковязкие ЯБ массы с низким расходом воды затворения. На рис. 12 приведены результаты исследований по кинетике нарастания пластической прочности массивов, сформированных в различных условиях (табл.2.).
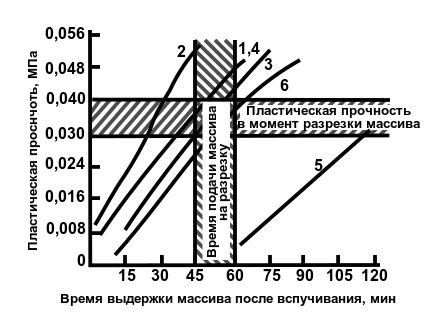
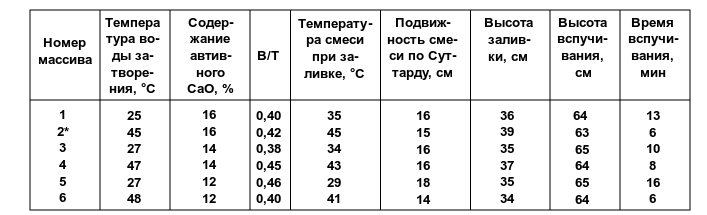
* Наблюдалось локальное кипение массы до завершения вспучивания.
Наиболее высокое качество разрезки наблюдалось у массива 6, который медленно набирал требуемую прочность. В остальных случаях скорость разогрева и конечная температура были недопустимо высокими. После заливки в ЯБ массе может начаться процесс так называемого ядрового разогрева. Примерно через 1 ч на расстоянии 2-5 см от бортов формы по сечению массива начинает наблюдаться разность температур, которая растет в направлении к геометрическому центру массива. Градиент температур связан с теплообменными процессами, происходящими между массивом и бортоснасткой. Низкий коэффициент теплопроводности поризуемой смеси, а также протекающие в ней экзотермические процессы газообразования и гидратации вяжущих способствуют увеличению перепада температур.
Данный эффект также может сказываться и на равномерности набора структурной прочности массива: в центре массива структурная прочность может соответствовать прочности, необходимой для резки, или даже превышать ее, а по краям массив может "плыть". Это явление особенно часто проявляется в массиве кубической формы (все размеры примерно равны), в меньшей степени – в массиве, имеющем форму бруса (два линейных размера одинаковы). Таким образом, оптимальной формой массива является пластина (a ≠ b>>l). Зоны повышенной прочности в теле массива могут стать причиной обрыва режущих струн. Более того, такие зоны часто являются очагами значительных структурных напряжений, возникающих при автоклавной обработке, и приводят к микротрещинообразованию и снижению прочности и эксплуатационной стойкости изделий. Указанные негативные явления обычно имеют место в тех случаях, когда температура в цехе опускается ниже +18°С, либо заливку осуществляют в холодные формы (с температурой менее 15°С). В этой связи было предложено осуществлять вызревание ЯБ массивов в специальных туннелях с регулируемой влажностью и температурой, которые целесообразно поддерживать на уровне 65-75% и 55-60 °С соответственно. Ввод добавок способен оказывать положительное влияние на процессы схватывания и твердения. Добавка гипса позволяет получить более стабильные цементирующие вещества, но при этом растягиваются сроки гидратации извести; снижается воздухоудерживающая способность массы. Иногда сужается интервал оптимальных температурно-влажностных показателей, приводя к ложному кипению и другим видам ухудшения макроструктуры материала. Добавки глиежа, цемянки, дисперсных зол и т.п. повышают пластичность массы. Однако при этом увеличивается водопотребность и усадочные деформации, что отрицательно сказывается на трещиностойкости изделий. Введение в состав шихты поверхностно-активных и воздухововлекающих веществ улучшает процессы порообразования. Граничные параметры области 1 (рис. 8.11) значительно расширяются при использовании в шихте шлакопортландцемента или молотого гранулированного шлака в количестве 50-70 кг на 1 м 3 изделий. При этом улучшается макро- и микроструктура ячеистого бетона. На современных заводах макро- и микроструктуру ЯБ контролируют в автоматическом режиме (рис. 13.).
Наиболее высокое качество разрезки наблюдалось у массива 6, который медленно набирал требуемую прочность. В остальных случаях скорость разогрева и конечная температура были недопустимо высокими. После заливки в ЯБ массе может начаться процесс так называемого ядрового разогрева. Примерно через 1 ч на расстоянии 2-5 см от бортов формы по сечению массива начинает наблюдаться разность температур, которая растет в направлении к геометрическому центру массива. Градиент температур связан с теплообменными процессами, происходящими между массивом и бортоснасткой. Низкий коэффициент теплопроводности поризуемой смеси, а также протекающие в ней экзотермические процессы газообразования и гидратации вяжущих способствуют увеличению перепада температур.
Данный эффект также может сказываться и на равномерности набора структурной прочности массива: в центре массива структурная прочность может соответствовать прочности, необходимой для резки, или даже превышать ее, а по краям массив может "плыть". Это явление особенно часто проявляется в массиве кубической формы (все размеры примерно равны), в меньшей степени – в массиве, имеющем форму бруса (два линейных размера одинаковы). Таким образом, оптимальной формой массива является пластина (a ≠ b>>l). Зоны повышенной прочности в теле массива могут стать причиной обрыва режущих струн. Более того, такие зоны часто являются очагами значительных структурных напряжений, возникающих при автоклавной обработке, и приводят к микротрещинообразованию и снижению прочности и эксплуатационной стойкости изделий. Указанные негативные явления обычно имеют место в тех случаях, когда температура в цехе опускается ниже +18°С, либо заливку осуществляют в холодные формы (с температурой менее 15°С). В этой связи было предложено осуществлять вызревание ЯБ массивов в специальных туннелях с регулируемой влажностью и температурой, которые целесообразно поддерживать на уровне 65-75% и 55-60 °С соответственно. Ввод добавок способен оказывать положительное влияние на процессы схватывания и твердения. Добавка гипса позволяет получить более стабильные цементирующие вещества, но при этом растягиваются сроки гидратации извести; снижается воздухоудерживающая способность массы. Иногда сужается интервал оптимальных температурно-влажностных показателей, приводя к ложному кипению и другим видам ухудшения макроструктуры материала. Добавки глиежа, цемянки, дисперсных зол и т.п. повышают пластичность массы. Однако при этом увеличивается водопотребность и усадочные деформации, что отрицательно сказывается на трещиностойкости изделий. Введение в состав шихты поверхностно-активных и воздухововлекающих веществ улучшает процессы порообразования. Граничные параметры области 1 (рис. 8.11) значительно расширяются при использовании в шихте шлакопортландцемента или молотого гранулированного шлака в количестве 50-70 кг на 1 м 3 изделий. При этом улучшается макро- и микроструктура ячеистого бетона. На современных заводах макро- и микроструктуру ЯБ контролируют в автоматическом режиме (рис. 13.).
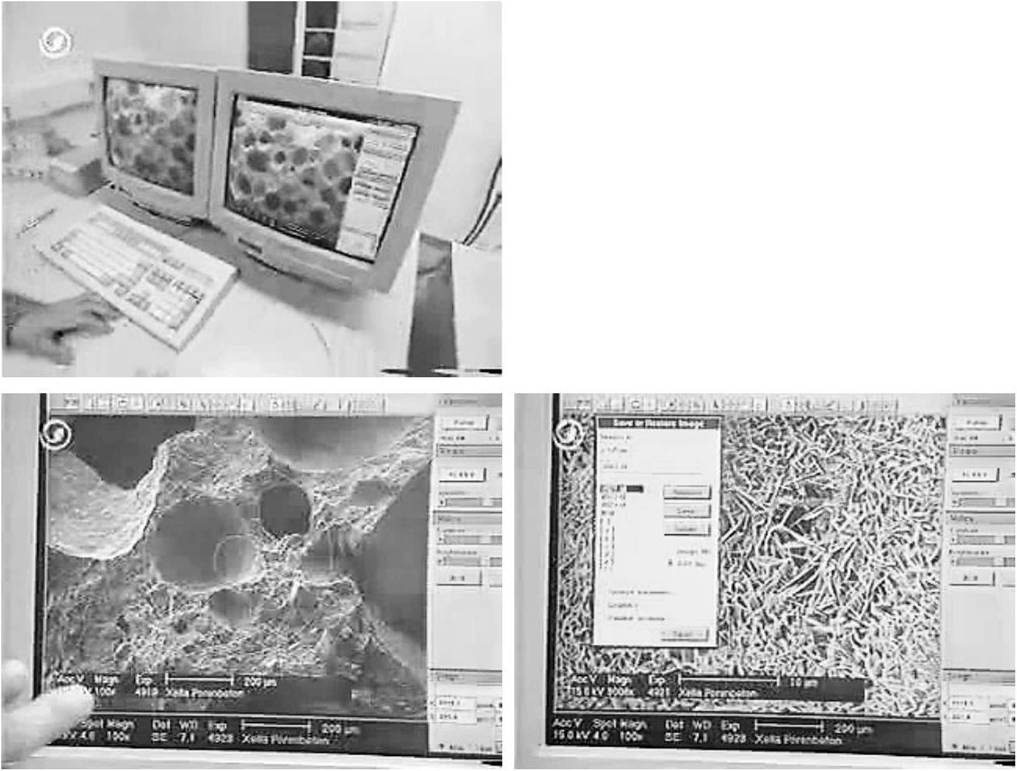
Процесс резки массива
При разрезке сырца ЯБ массива на изделия заданных размеров на лицевой (резаной) поверхности образуется деформированный слой, физические свойства которого зависят от пластической прочности сырца, диаметра режущей струны, скорости и режима резки (подвижная пилящая или неподвижная струна) и ряда других параметров. При продавливании струны определенного диаметра через толщу массива перед режущим органом образуется зона сжатия, в которой материал, испытывая дополнительное давление, деформируется и заполняет прилегающие поры и капилляры материала. Величина лобового сопротивления материала RL при встречном движении со струной приближенно может быть выражена соотношением нагрузки P к площади сопротивления струны, внедряемой перпендикулярно оси цилиндра:

где Rp – удельное сопротивление резки, Па; PT – пластическая прочность, определяемая пластометром с конусом 45 о , Па; a – коэффициент, зависящий от диаметра проволоки; при диаметре 0,5-1,5 мм а = 8-5. Опытным путем установлено, что скорость движения режущих струн мало влияет на удельное сопротивление. Обычно применяемая скорость фронтального движения режущего органа или скорость подачи материала на струну при неподвижном режущем органе составляет 1-4 м/мин. Определение величины удельного сопротивления материала резанию позволяет установить требуемую прочность режущей струны или по характеристикам струны рассчитать обратную задачу – максимально допустимую пластическую прочность сырца ячеистого бетона, при которой не произойдет обрыва струн. Для этой цели может быть использовано уравнение "веревочной параболы" в интерпретации И.А. Иванова:
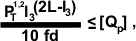
где L – длина струны; l3 – длина контакта струны с материалом; f – прогиб струны в пределах контакта; σp – допускаемое напряжение материала струны на разрыв. Для расчета нормального усилия в режущем органе и определения возникающих напряжений в струне производят замеры стрел прогиба струн путем отпечатывания их следов на незатвердевшем массиве и перенесения полученных кривых на бумагу. Результаты опытных определений указанных величин представлены на рис. 8.14. От прогиба струны зависит как геометрическая точность изделий, так и качество (чистота) разрезаемой поверхности, а также величины выколов в местах выхода режущей струны. При больших значениях прогиба напряжение растяжения в струне уменьшается, а при малых значениях прогиба при тех же нагрузках – возрастает. При внедрении струны в материал, независимо от пластической прочности сырца, сопротивление резке возрастает пропорционально величине деформаций.

Во время резки материал должен проскальзывать мимо струны, но, согласно теории пластичности, скольжение материала относительно струны может осуществляться тогда, когда коэффициент трения μ ≤ 0,5, так как в противном случае скольжение сопровождается разрушением поверхностного слоя. Одной из сложностей резки является неравномерное твердение сырца в форме после завершения вспучивания. Это обусловлено в основном существенной разницей температур в центре и поверхностных слоях массива в процессе созревания, а также часто наблюдаемым различием плотности по высоте массива. В результате в теле массива появляются зоны повышенной прочности, которые являются основной причиной обрыва режущих струн (рис. 15.).
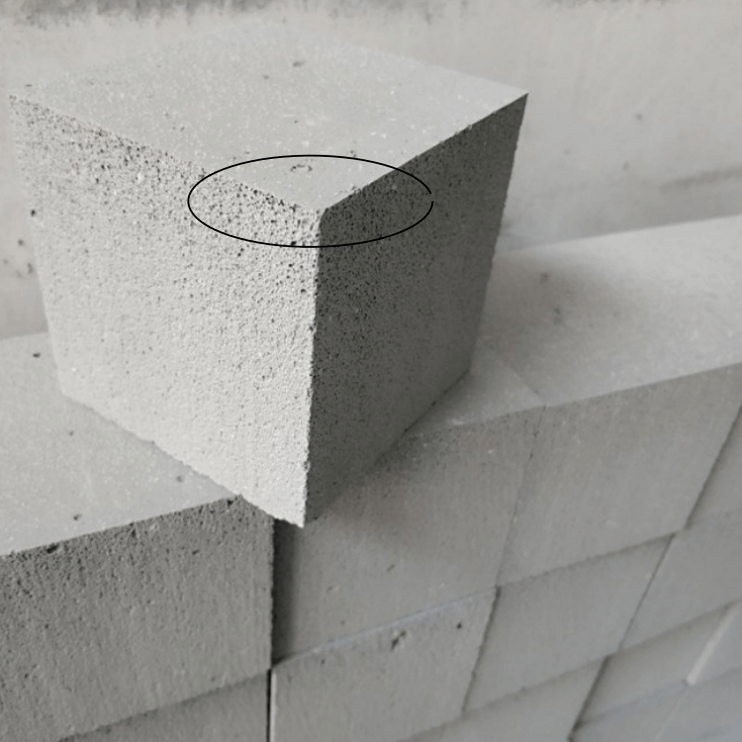