Известь
В качестве основного вяжущего применяют кальциевую строительную известь воздушного твердения, отвечающую требованиям ГОСТ 9179 "Известь строительная. Технические условия". Влажность гидратной извести должна быть не более 5%. Рекомендуется использовать негашеную известь-кипелку не ниже 2-го сорта с содержанием активных СаО и MgO не менее 70-80%, пережога – не более 2 %.
Если для производства силикатного кирпича идеальной является известь мягкого и среднего обжига с высокой реакционной способностью (время гашения 1-4 мин до достижения 60 оС), то для производства газобетона необходима известь сильного или среднего обжига. Эта известь имеет малую активность (время гашения 4-7 (12) мин до достижения 60 ºС), что способствует равномерному, медленному росту газобетонной смеси в форме. Сроки гашения извести должны составлять 15-25 мин. Скорость гашения существенно влияет на тепловыделение (рис.1), необходимое для правильного формирования структуры.
Если для производства силикатного кирпича идеальной является известь мягкого и среднего обжига с высокой реакционной способностью (время гашения 1-4 мин до достижения 60 оС), то для производства газобетона необходима известь сильного или среднего обжига. Эта известь имеет малую активность (время гашения 4-7 (12) мин до достижения 60 ºС), что способствует равномерному, медленному росту газобетонной смеси в форме. Сроки гашения извести должны составлять 15-25 мин. Скорость гашения существенно влияет на тепловыделение (рис.1), необходимое для правильного формирования структуры.
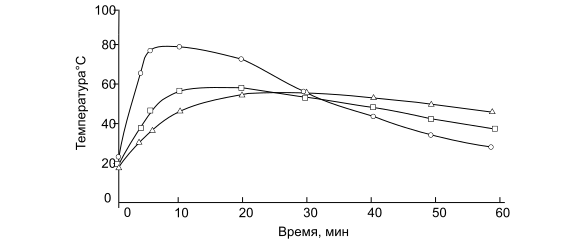
Содержание MgO не должно превышать 5%; для ячеистых бетонов желательно не выше 3%. В ряде стран в производстве автоклавных ЯБ применяют известь с очень высокой активностью, например, в Чехии содержание активных СаО+MgO должно быть не менее 94%. При этом чешский стандарт так лимитирует скорость роста температуры: за 2 мин температура должна повыситься с 25 до 55ºС, а за 6-15 мин – до 60-80ºС. По рекомендациям компании "HESS ACC" молотая негашеная известь для ЯБ должна содержать, мас. %: СаО – 75; MgO до 2; CO2 – 4; SO3 – до 3; Na2O – до 1,5; потери массы при прокаливании – до 5; проход через сито № 01 – 95% /остаток на сите № 009 – до 8. Время гашения до 60ºС 4-10 мин. Активность, характеризуемая повышением температуры, приведена в табл. 1.
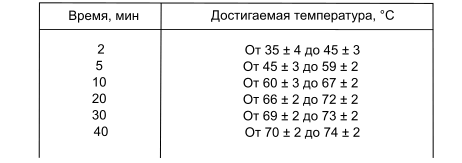
Примечание. Условия: 600 см3 дистиллированной воды при (20±0,5)°C и (150±0,1) г негашеной извести.
В требования компании "W+K" входят следующие показатели: содержание СаО – не менее 90, MgO – не более 3 мас. %; потери массы при прокаливании – до 5; остаток на сите № 009 – до 6, на сите № 0063 – до 15, на сите № 0032 – до 50 мас. %. Известь не должна образовывать агломераты. Время гашения до 60 ºС 8-12 мин. При использовании высокоэкзотермической извести с температурой гашения около 85ºС в процессе приготовлении ячеистобетонной массы выделяется большое количество теплоты, что способствует процессу порообразования, предотвращению оседания газонасыщенной массы до ее затвердевания и повышению прочности готовых изделий ячеистой структуры. Известь должна иметь тонкий помол, так как высокая дисперсность обеспечивает хороший контакт СаО с кремнеземом и интенсивное их взаимодействие. Важнейшим показателем вяжущего является постоянство его характеристик, так как нестабильность свойств нарушает технологический процесс, приводя к колебаниям материального состава смеси. Изменяются также реологические характеристики формовочной смеси, кинетика синтеза и формирования структуры цементирующих веществ при автоклавной обработке, динамика нарастания прочности и макроструктура конечного ячеистого бетона.
В требования компании "W+K" входят следующие показатели: содержание СаО – не менее 90, MgO – не более 3 мас. %; потери массы при прокаливании – до 5; остаток на сите № 009 – до 6, на сите № 0063 – до 15, на сите № 0032 – до 50 мас. %. Известь не должна образовывать агломераты. Время гашения до 60 ºС 8-12 мин. При использовании высокоэкзотермической извести с температурой гашения около 85ºС в процессе приготовлении ячеистобетонной массы выделяется большое количество теплоты, что способствует процессу порообразования, предотвращению оседания газонасыщенной массы до ее затвердевания и повышению прочности готовых изделий ячеистой структуры. Известь должна иметь тонкий помол, так как высокая дисперсность обеспечивает хороший контакт СаО с кремнеземом и интенсивное их взаимодействие. Важнейшим показателем вяжущего является постоянство его характеристик, так как нестабильность свойств нарушает технологический процесс, приводя к колебаниям материального состава смеси. Изменяются также реологические характеристики формовочной смеси, кинетика синтеза и формирования структуры цементирующих веществ при автоклавной обработке, динамика нарастания прочности и макроструктура конечного ячеистого бетона.
Портландцемент
Для производства ЯБ рекомендуется портландцемент (ПЦ) марки М400- 500, не содержащий активных минеральных добавок. Содержание алита в ПЦ – не менее 50%, трехкальциевого алюмината 5-8% ("HESS" – не менее 6%). Начало схватывания не позднее 2 ч, конец – 2-4 ч. Удельная поверхность цемента – не менее 300 м 2 /кг. Компания "HESS ACC" дает следующие рекомендации. Удельная поверхность ПЦ (по Блейну) – 350-400 м²/кг. Сроки схватывания, мин: 120-260 (начало); 300 (конец). Прочность на сжатие образца в форме куба, МПа: 3 сут – 20-25; 7 сут – 30-35; 28 сут – 40-45. Щелочность – 0,4-0,8%. К требованиям компании "W+K" относятся: класс прочности для ПЦ – CEM I/32.5 или CEM I/42.5; содержание, мас. %: С3S – не менее 50; С3А – 6-12; С4AF – до 10; Na2O+K2O – до 1; MgO – до 3. Остаток на сите № 0032 – до 30%. Удельная поверхность (по Блейну) – 250-450 м²/кг. Сроки схватывания, мин: 80-180 (начало); 140-260 (конец). Водопотребность – 25-30%. П.И. Боженов и А.А. Федин отмечали целесообразность использования шлакопортландцемента (ШПЦ) вместо портландцемента. Замена цемента гранулированным шлаком в оптимальном соотношении снижает усадочные деформации, то есть повышает трещиностойкость силикатных ЯБ. По данным ряда зарубежных фирм, суточная прочность ШПЦ должна составлять 13-15 МПа. Вяжущие обычно завозят автотранспортом и разгружают в силосы хранения или непосредственно в расходные силосы.
Гипс или ангидрит
Для замедления гашения извести-кипелки и стабилизации структуры поризованной массы добавляют двуводный гипс (ГОСТ 4013) или ангидрит, измельченный до остатка на сите № 02 не более 3%. Допускается применение полуводного гипса с добавкой поташа. При определении дозировки гипса следует учитывать тот факт, что он снижает водоудерживающую способность смеси. По рекомендациям компании "HESS ACC" гипс должен содержать, мас. %: сульфат кальция – 80, MgO – до 2, хлориды – до 0,05. Компанией "W+K" установлены требования по содержанию SO3, мас.%: не менее 40 – при использовании дигидрата CaSO4∙2H2O, не менее 53 – для ангидрита CaSO4. Регламентировано также количество CaS – до 0,5 мас.% и Cl – до 150 мг/кг. Гипс может поступать на завод в виде кусков различных фракций (обычно до 30 мм) или порошка. В первом случае материал размалывают вместе с песком в шаровой мельнице, а во втором – его дозируют непосредственно в смеситель. Имеется информация о том, что добавка гипса в количестве от 1 до 5% резко интенсифицирует процесс связывания оксида кальция с кремнеземом.
Кремнеземистый компонент
На долю кремнеземистого компонента приходится более 60 % по массе и до 75 % по объему твердой фазы. В качестве кремнеземистого компонента используют кварцевый песок, золы ТЭС, шлаки и др. Важнейшими показателями кремнеземистого компонента в составе смеси для производства ЯБ являются: содержание SiO2, гранулометрический состав и содержание нежелательных примесей (пылевидных и глинистых частиц).
Кварцевый песок
Основным видом кремнеземистого сырья является кварцевый песок преимущественно с содержанием 85-95% свободного кварца (не менее 70%), оптимально – более 90% SiO2; количество илистых и глинистых примесей не более 3-5%, слюды не более 0,5%. Содержание монтмориллонита – не более 1%. По остальным показателям песок должен удовлетворять ГОСТ 8736. Для автоклавных бетонов содержание сернистых и сернокислых соединений в пересчете на SO2 должно быть не более 2%; щелочей (в пересчете на Na2O) – не более 0,9%; пылевидных, илистых и глинистых частиц размерами менее 0,05 мм – не более 0,5%; зерен размером более 5 мм – не более 5 %. Средняя насыпная плотность 1500-1550 кг/м 3 . В кварцевом песке не допускается наличие зерен более 10 мм в количестве свыше 0,5%, а более 5 мм – свыше 10% по массе. Количество частиц менее 0,16 мм не должно превышать 10 и 15% соответственно для крупных и мелких песков. Требования к кварцевому песку в соответствии с рекомендациями компании "HESS ACC", мас. %: SiO2 более 85; Fe2O3 до 3; Al2O3 до 7-10; СаО до 10; MgO до 2; SO3 до 3; Na2O – до 2; слюда – до 0,5; потери массы при прокаливании – до 5; хлориды – до 0,05; глинистые и илистые – до 3. Требования компании "W+K", мас. %: SiO2 не менее 90; Fe2O3 до 3; Al2O3 до 4; СаО до 6; MgO до 3; SO3 до 3; Na2O – до 0,5; К2О – до 1,5; потери массы при прокаливании – до 5; хлориды – до 0,02; глинистые минералы – не допускаются. Если содержание SiO2 меньше 90%, то требуются дополнительные лабораторные испытания для оценки качества песка. Зернистость загружаемого песка – 0-3 мм. Влажность – до 7%. Завезенный на завод автомобильным или железнодорожным транспортом песок хранят на открытом или закрытом складе, расположенном вблизи отделения мельниц.
Зола-унос
В ряде стран, в частности в Польше, в качестве кремнеземистого компонента широко используют золу-унос ТЭС. Требования, предъявляемые к золе, прежде всего, касаются содержания СаО, стекловидных и оплавленных частиц. Зола должна содержать не менее 40- 45% SiO2. Потеря массы при прокаливании для зол, получаемых сжиганием антрацита и каменного угля, не должна превышать 8 %, для остальных зол – до 5%; удельная поверхность – 200-300 м 2 /кг. По рекомендациям компании "HESS ACC" используемая зола должна иметь следующие характеристики, %: содержание SiO2 – 50, в том числе активный SiO2 – 25; Fe2O3 – 18; Al2O3 – 35; СаО – 7; SO3 – 2; Na2O – 1,5; потери массы при прокаливании – 7,0; остаток на сите № 0063 – 25. Удельная поверхность – 200-500 м²/кг. Насыпная масса - 600-1000 кг/м3 . Водопотребность – 40%. Радиоактивность – не выше 150 Бк/кг. Зола отличается неоднородностью химико-минералогического состава, высокой пористостью и дисперсностью. Эти особенности золы способствуют повышению влагоемкости и замедленной водоотдаче бетона, его пониженной трещиностойкости. К преимуществам золы можно отнести возможность ее применения в отдельных случаях без предварительного размола. Это позволяет получать изделия меньшей плотности, чем с кварцевым песком. Золу доставляют в грузовых автомобилях и высыпают в приемный резервуар, который уже наполнен необходимым количеством воды. Вмонтированная мощная мешалка перемешивает смесь, пока не образуется производственный шлам необходимой плотности. Несмотря на высокую дисперсность (~ 500 м2 /кг для каменноугольной золы), с целью уменьшения внутренней пористости и гомогенизации зо́лы, как правило, подвергают дополнительному помолу. Прежде всего, это относится к золам гидроудаления. Зола по сравнению с песком является химически более активной, что обусловлено высоким содержанием стеклофазы. В г. Новомичуринске (Рязанская обл.) ведется строительство газобетонного завода в непосредственной близости от тепловой электростанции. Линия кремнеземистого компонента будет оснащена оборудованием как для использования золы уноса и золы с золоотвала электростанции, так и для песка. Другие кремнеземистые компоненты (трепел, опоку и т.п.), имеющие повышенную водопотребность, для ЯБ практически не используют.
Газообразователи
За последние годы требования производителей ЯБ к газообразователям существенно возросли. Это связано, в первую очередь, с введением в строй более двух десятков предприятий, оснащенных современным высокопроизводительным оборудованием фирм "Wehrhahn", "Masa-Henke", "Xella", "W+K", "Hess" и др. Наиболее распространенными добавками, приводящими к газовыделению, являются пудры и пасты, содержащие алюминий. Протекающую реакцию газовыделения можно описать уравнением: 2Al + 3Сa(OH)2 + 6Н2О = 3CaO∙Al2O3∙6Н2О + 3H2↑. В результате химической реакции между алюминием и гидроксидом кальция 1 г Al при температуре 25-30 ºС выделяет 1390 см 3 водорода.
Алюминиевая пудра
Алюминиевая пудра занимает бо́льшую часть рынка газообразователей, а опыт ее применения насчитывает уже около ста лет. В технологии ГБ изделий в качестве газообразователей главным образом используют алюминиевую пудру марок ПАП-1 и ПАП-2, отвечающую требованиям ГОСТ 5494-95 "Пудра алюминиевая пигментная. Технические условия" (табл. 5.2) с содержанием активного алюминия 91,1-93,9% и временем активного (максимума) газовыделения в течение 3-4 мин от начала смешивания компонентов газобетонной массы.
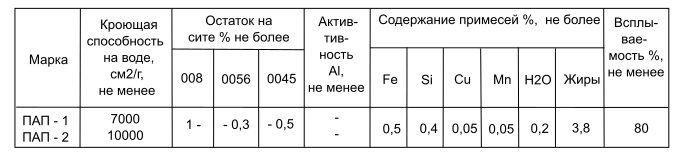
Применяют также пудру ПАК-3 или ПАК-4, содержащую 82 % активного Al.
К пудре предъявляют требования по дисперсности – 460-600 м2 /кг, так как с дисперсностью связан процесс протекания газообразования в ЯБ смеси. Примерный гранулометрический состав алюминиевой пудры приведен на рис 2.
К пудре предъявляют требования по дисперсности – 460-600 м2 /кг, так как с дисперсностью связан процесс протекания газообразования в ЯБ смеси. Примерный гранулометрический состав алюминиевой пудры приведен на рис 2.

Существенным фактором, влияющим на формирование однородной структуры газобетона, является однородность частиц Al по размеру. Полидисперсный состав пудр ("широкие" пудры) ухудшает структуру ячеистого бетона и вызывает перерасход газообразователя. Кинетика газовыделения двух типов пудр представлена кривыми на рис. 3.
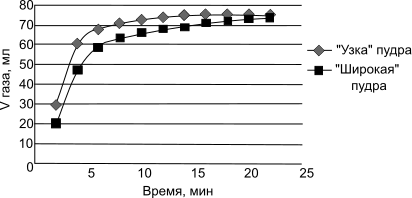
Полное окончание газовыделения пудр с узким фракционным составом ("узких" пудр) происходит на 5-10 мин раньше по сравнению с "широкими" пудрами. По рекомендациям компании "HESS ACC", порошок алюминия должен содержать активный металл в количестве 90-95%. Максимальное количество надситного материала 45 мкм – 20-50%. Средний размер зерна – 20-45 мкм. Удельная поверхность по Блейну – 1000-2000 м²/кг. Максимальное содержание жирных кислот – 1,5%. Газовыделение при введении пудры в смесь должно начинаться через 1-2 мин и продолжаться 15-20 мин. Максимальное выделение водорода происходит при температуре смеси 30-40ºС. Расход Al-пудры составляет 0,5-1,4 кг на 1 м3 газобетона. Однако контроль таких показателей, как кинетика газовыделения и содержание активного алюминия, со стороны производителей пудры отсутствует, то есть качество оценивается, в первую очередь, с точки зрения использования продукта в производстве лакокрасочной продукции, твердых сплавов и т.п. К недостаткам пудры также относится высокое пыление и пожароопасность, которые обусловливают необходимость дополнительных мер безопасности и применения ПАВ в процессе приготовления алюминиевой суспензии. Алюминиевую пудру хранят в герметичной металлической таре. Поверхность частиц пудры покрыта оболочкой, состоящей из нескольких слоев ориентированных молекул жирных кислот и продуктов их взаимодействия с оксидом алюминия – стеаратов Al. Этот факт, наряду с пластинчатой формой частиц алюминия, является причиной всплывания пигментных пудр на поверхность воды с образованием чешуйчатого покрова, что делает невозможным их непосредственное применение в технологии ЯБ. Для удаления с поверхности частиц жирной пленки пудры обрабатывают поверхностно-активными веществами (ПАВ) или прокаливают в электропечах (200-220ºС, 4-6 ч, слой толщиной 4 см). В заводских условиях смачиваемость порошка в процессе получения водной алюминиевой суспензии обычно обеспечивают обработкой ПАВ, в частности сульфанолом, мылонафтом и др. Расход ПАВ (в пересчете на сухое вещество) составляет ~5% от массы пудры. Сульфанол – алкилбензолсульфонат (смесь изомеров натриевых солей алкилбензолсульфокислот) с общей формулой R-C6H4NaO3S, где R – радикал, соответствующий общей формуле СnH2n+1, n=14-18.
Принципиальную формулу сульфанола можно представить в виде:
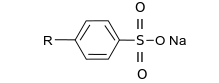
Сульфанол должен удовлетворять требованиям ТУ 6-01-1001-77. Сульфанол обладает свойствами ПАВ; его берут из расчета 25 г на 1 л воды. В пигментной пудре могут присутствовать комки, состоящие из сваренных между собой алюминиевых частиц. При приготовлении алюминиевой суспензии подобные частицы не отделяются друг от друга, и вводимое ПАВ обволакивает укрупненные агломераты. Наличие комков не позволяет получить однородную структуру ячеистого бетона. Образующиеся ячейки больших размеров имеют далекую от идеальной сферы форму, а также склонны к объединению при вспучивании массива. Нестабильность свойств пигментной пудры привела к необходимости разработки новых видов газообразователей, в частности гидрофильных пудр. Процесс производства гидрофильных Al пудр осуществляют в атмосфере инертного газа (азота) с контролируемым содержанием кислорода. Для придания пудре гидрофильных свойств, предупреждения сваривания алюминиевых частиц, а также уменьшения пыления конечного продукта и сокращения времени приготовления алюминиевой суспензии, в процессе измельчения в мельницу подают комплексную добавку. Одним из компонентов этой добавки является ПАВ. Подача ПАВ непосредственно в мельницу позволяет добиться его равномерной адсорбции на алюминиевых частицах, исключая присутствие укрупненных агломератов (склеенных комков). Лидером в области выпуска и реализации алюминиевых гидрофильных пудр (табл. 5.3) является Объединенная компания (ОК) РУСАЛ, которая в 2011 г. реализовала 6 740 т алюминиевых компонентов для производства газобетонных изделий на рынке стран СНГ.
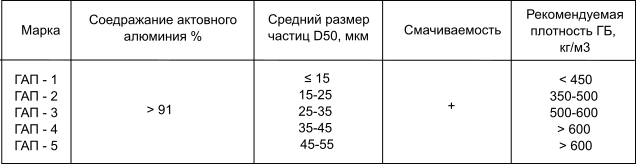
Пудры ГАП отличаются кинетикой газовыделения (рис. 4.).
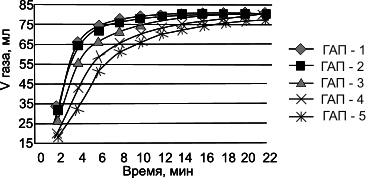
Продукты со средним размером частиц < 15 мкм оптимальны при производстве газобетона плотностью менее 450 кг/м3 .
Алюминиевые газопасты
В настоящее время большинство современных технологических линий по производству газобетона ориентировано на применение Al паст. Активное применение паст в России началось в 2005 г.; в настоящее время их доля в общем объеме газообразователей составляет 27-33%.
В пасте содержание активного алюминия – не менее 60%; остаток на сите № 008 не допускается. При применении газопасты отпадает необходимость в добавлении ПАВ; она легко смачивается и перемешивается с водой, образуя суспензию, которая равномерно распределяется в бетонной массе без агрегатирования. При одинаковой общей пористости изделий средний размер пор в газобетоне в 2-2,5 раза меньше, чем в изделиях на пудре. Главными преимуществами работы с пастами является практически полное отсутствие пыления, а значит, пасты пожаро- и взрывобезопасны, отвечают современным санитарно-гигиеническим нормам условий труда. Отрицательным эффектом применения газопасты по сравнению с алюминиевой пудрой является удлинение сроков достижения пластической прочности на 15-30 мин. Кроме того, пасты имеют более высокую стоимость и повышенный расход. ОК РУСАЛ производит 15 видов паст, отличающихся гранулометрическим составом и содержанием сольвента (табл. 4.).
В пасте содержание активного алюминия – не менее 60%; остаток на сите № 008 не допускается. При применении газопасты отпадает необходимость в добавлении ПАВ; она легко смачивается и перемешивается с водой, образуя суспензию, которая равномерно распределяется в бетонной массе без агрегатирования. При одинаковой общей пористости изделий средний размер пор в газобетоне в 2-2,5 раза меньше, чем в изделиях на пудре. Главными преимуществами работы с пастами является практически полное отсутствие пыления, а значит, пасты пожаро- и взрывобезопасны, отвечают современным санитарно-гигиеническим нормам условий труда. Отрицательным эффектом применения газопасты по сравнению с алюминиевой пудрой является удлинение сроков достижения пластической прочности на 15-30 мин. Кроме того, пасты имеют более высокую стоимость и повышенный расход. ОК РУСАЛ производит 15 видов паст, отличающихся гранулометрическим составом и содержанием сольвента (табл. 4.).
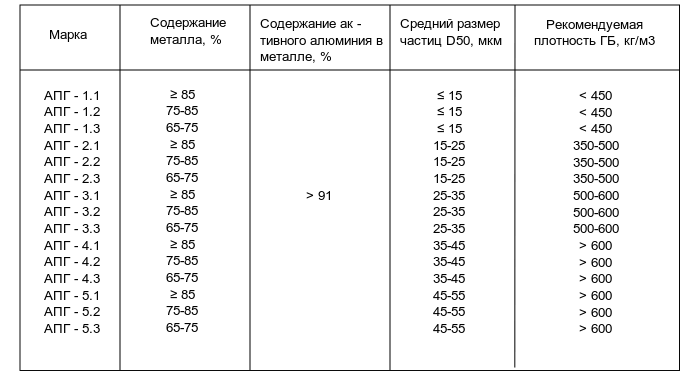
При переходе от ГАП-2 к АПГ-2.3 расход газообразователей растет, а пыление снижается, что вызвано увеличением содержания сольвента (табл. 5.). При этом количество выделяемого водорода уменьшается без изменения кинетики газовыделения (рис. 5.). Технологические особенности применения паст не отличаются от описанных выше особенностей применения алюминиевых гидрофильных пудр.
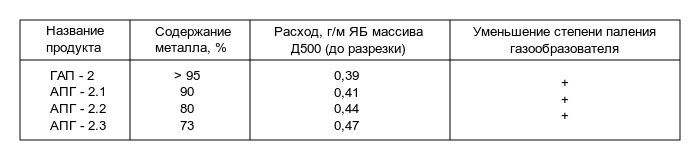
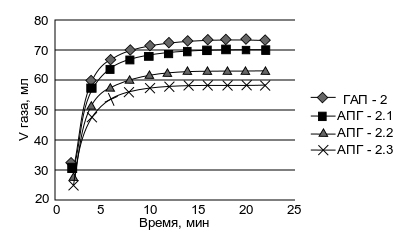
Al-содержащие продукты ООО "Нордстройкомплект-ТЕК"
В 2005 г. по итогам международной конференции "Перспективы развития глубокой переработки алюминия" была утверждена отраслевая программа "Российские алюминиевые газообразователи". Основным разработчиком стало ООО "Нордстройкомплект-ТЕК" ("НСК-ТЕК"). В 2007 г. была запущена в серийное производство линия алюминиевых газообразователей марок "Газобетолайт" (ТУ 1791-001-75754739-2006), "Газобетолюкс" (ТУ 1791-001-75754739-2006), "Газобетопласт". С 2010 г. начат выпуск газообразователей с несвязанной структурой "Газобето+500" и "Газобето+400" (СТО 75754739-001-2010), которые соединили в себе преимущества паст и экономичность пудр. В 2011 г. "НСК-ТЕК" уже занял более 30% российского рынка газобетона по использованию газообразователей, в первую очередь марок "Газобето", в т.ч. более 70% паст. Специализированные газообразователи для производства газобетона гидрофильны, что исключает необходимость применения ПАВ.
Добавки "Газобето+" дифференцированы по маркам в зависимости от требуемой плотности готовой продукции. Они представляют собой тонкоизмельченный Al порошок серебристо-серого цвета, с пониженным пылением при пересыпании. Частицы Al после обработки органическими добавками образуют непрочные конгломераты, которые легко разрушаются при контакте с водой. В то же время этой прочности достаточно, чтобы значительно снизить пыление порошка. Низкая степень пыления исключает вероятность воспламенения или взрыва в зоне приготовления суспензии. Высокая активность "Газобето+" значительно (на 25-35 % по сравнению с зарубежными аналогами-пастами) сокращает расход газообразователя. В сертификат качества "Газобето+" включены необходимые для заводских технологов характеристики: кинетика газовыделения, содержание активного алюминия, смачиваемость (табл. 6.). Срок хранения готовой продукции 1 год, в составе суспензии – 72 ч
Добавки "Газобето+" дифференцированы по маркам в зависимости от требуемой плотности готовой продукции. Они представляют собой тонкоизмельченный Al порошок серебристо-серого цвета, с пониженным пылением при пересыпании. Частицы Al после обработки органическими добавками образуют непрочные конгломераты, которые легко разрушаются при контакте с водой. В то же время этой прочности достаточно, чтобы значительно снизить пыление порошка. Низкая степень пыления исключает вероятность воспламенения или взрыва в зоне приготовления суспензии. Высокая активность "Газобето+" значительно (на 25-35 % по сравнению с зарубежными аналогами-пастами) сокращает расход газообразователя. В сертификат качества "Газобето+" включены необходимые для заводских технологов характеристики: кинетика газовыделения, содержание активного алюминия, смачиваемость (табл. 6.). Срок хранения готовой продукции 1 год, в составе суспензии – 72 ч
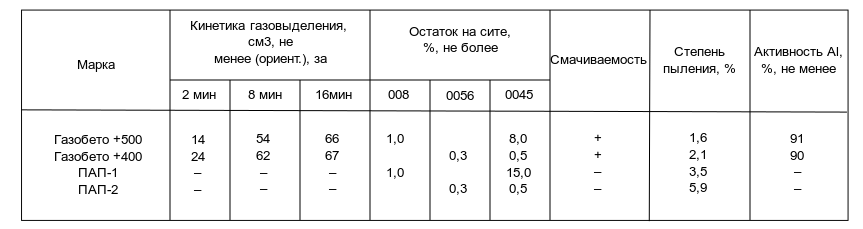
По данным производителя, по истечении гарантийного срока хранения "Газобето+" (18 месяцев) происходит незначительное (до 3%) снижение активности. "Газобето+500" применяют для производства блоков с плотностью D500- D600. Время приготовления суспензии – 30-40 мин при концентрации 1/20- 1/10. Время роста массива составляет: 6-8 мин на ударной и до 20 мин на литьевой технологии. Конечная фаза газовыделения сопровождается мелкими, кратковременными выхлопами почти без просадки (до 0,5 см). Средний расход добавки для D500 составляет 0,36-0,46 кг/м 3 , для D600 – 0,3-0,4 кг/м 3 . Для выпуска газобетона плотностью D350-D400 используют "Газобето+400" с расходом 0,43-0,6 кг/м 3 . Процесс формирования массива характеризуется небольшой просадкой (до 2,0 см) при кратковременных и спокойных выхлопах в конце газовыделения. После автоклавирования газобетон имеет равномерную мелкопористую структуру с классом по прочности D400 не ниже В2, D350 не ниже В1,5, что удовлетворяет требованиям ГОСТ 31360-2007. Добавки "Газобето+" успешно прошли испытания на ряде заводов, в числе которых ООО "ПСО Теплит" (Свердловская обл.), ЗАО "КСМ" (Тюменская обл.), ЗАО "ДЗГИ" (Московская обл.), ООО "НЗСМ" (Челябинская обл.), ООО "КПД-210" (Ростовская обл.), ОАО "Кирпич силикатный" (Республика Мордовия), ООО "Эко Блок" (Калининградская обл.).
Комплексный газообразователь
Комплексный газообразователь – смесь алюминиевой пудры и дисперсного ферросилиция (ферросплава). Соотношение пудры ПАП-1 и дисперсного ферросилиция ФС-75 находится в пределах от 1:4 до 1:1. Каждый компонент смеси является газообразователем, но имеет собственную скорость образования массы газа и абсолютную массу полученного газа. Ферросилиций является газообразователем второго действия. Реакция взаимодействия ферросилиция со щелочными компонентами смеси (по сравнению с Al) протекает медленнее, поэтому суммарная скорость образования водорода у комплексного газообразователя ниже, чем скорость образования той же массы газа у алюминиевой пудры. Общий расход комплексного газообразователя 0,25- 0,86 кг на 1 м3 ячеистого бетона плотностью 500-800 кг/м3 .
Корректирующие добавки
В качестве активных дисперсных минеральных наполнителей можно вводить микрокремнезем, тонкомолотые металлургические шлаки, цеолиты и др. Эффективной добавкой считают микрокремнезем – побочный продукт производства ферросилиция. Его основным компонентом является аморфный SiO2 (87-92%) с насыпной массой 0,2-0,3 г/см3 и удельной поверхностью 40- 50м 2 /г. В смеси с известью микрокремнезем проявляет свойства активной минеральной добавки, связывая до 7% гидроксида кальция в низкоосновные гидросиликаты кальция за 5-7 ч нормального твердения, а за 30 сут связывается до 1г Са(ОН)2 на 1 г микрокремнезема. Эта добавка позволяет снизить среднюю плотность ЯБ, практически не уменьшая прочности, то есть снизить расход вяжущего и газообразователей, сократить длительность технологической выдержки перед термообработкой, улучшить макроструктуру бетона. Расход добавки составляет 5-30% от массы сухих компонентов. Для регулирования процесса структурообразования, нарастания пластической прочности и ускорения твердения ЯБ смеси, а также ее пластификации используют двуводный гипс, кальцинированную соду, триэтаноламин, тринатрийфосфат, жидкое стекло, суперпластификаторы и др. В качестве добавок, ускоряющих твердение бетона, применяют сернокислый алюминий Al2(SO4)3 и хлористый кальций СаС12. Часть изделий подвергают гидрофобизации силиконовыми смолами.
Вода
Для приготовления газобетонной смеси используют водопроводную воду по ГОСТ 23732 "Вода для бетонов и растворов", в большинстве случаев – обычную питьевую воду из системы городского водоснабжения. Потребность в воде составляет от 0,5 до 1,5 м 3 /ч в зависимости от производительности линии. В случае применения технической воды из поверхностных источников она должна удовлетворять следующим условиям: несоленая (содержание всех солей не более 5000 мг/л); мягкая или средней жесткости (рН 4-12,5), не содержащая нефтепродуктов, жиров и масел, гуминовых соединений, сахаров. По рекомендациям компании "HESS ACC": рН – от 6,5 до 7,5; содержание хлорид-ионов – до 450 мг/л; содержание сульфат-ионов – до 150 мг/л; жесткость – до 18 dН (degrees of hardness), что соответствует 3,2 ммоль/л. Вода не должна содержать взвешенных частиц. Для технологического процесса обеспечивают подогрев воды до температуры 40-60°С. По данным компании "HESS ACC", температура производственной воды, °С: холодной – около 15; горячей – около 90.
Смазочные материалы
Смазку используют для создания разделительных жидких или пленочных покрытий, препятствующих сцеплению сырца ЯБ со сталью. Смазка должна удовлетворять следующим требованиям:
обеспечивать освобождение изделий из форм без повреждений;
не допускать загрязнения поддона и бортов формы остатками бетона;
не вызывать коррозии металлических форм;
быть недефицитной и несложной по технологии изготовления и нанесения;
быть безопасной в пожарном отношении;
быть однородной по составу и консистенции в процессе хранения;
хорошо удерживаться на вертикальных поверхностях форм;
образовывать сплошную пленку возможно меньшей толщины;
иметь низкую растворимость в воде, не проникать в поверхностный слой бетона и не оставлять жировых пятен;
быть безвредной для человека;
обладать устойчивостью при многократной оборачиваемости форм;
не высыхать и не терять качества в течение установленного времени.
Правильно выбранная смазка облегчает распалубку изделий и способствует получению ровной поверхности массивов без масляных пятен. Для смазки форм используют смеси составов со следующими массовыми соотношениями: петролатум – керосин 1:2,5; солидол / автол – керосин 1:1; кулисное и машинное масло 1:3; эмульсолы и др. В 2006 г. в Институте природопользования НАН Беларуси совместно с ОАО "Завод горного воска" разработана и внедрена в производство смазка "Бетол-01". В качестве основы смазки используют высоковязкие минеральные и растительные масла. Для обеспечения эксплуатационных свойств смазки в ее состав вводят комплекс антиадгезионных, вытесняющих, моющих и защитных присадок. Наличие в смазке маслорастворимых ПАВ позволяет создать на горизонтальных и вертикальных поверхностях опалубки прочный разделительный слой, обладающий высокими антиадгезионными свойствами (относительная величина снижения адгезии бетона к стали составляет не менее 97%). В состав смазки также введен маслорастворимый ингибитор коррозии на основе остаточного продукта крекинга масляных фракций. Форму, покрытую смазкой, можно длительное время хранить на открытом воздухе без потери ее потребительских свойств. По показателям кинематической вязкости при 40°С смазка "Бетол-01" соответствует диапазону 90-110 сСт (марка А) и 110-150 сСт (марка Б). Высокие эксплуатационные свойства смазки "Бетол-01" продлевают срок службы опалубки, защищая ее от коррозии. По комплексу эксплуатационных характеристик смазка "Бетол-01" не уступает немецкой смазке Addinol F150, однако существенно дешевле. Смазку наносят на внутреннюю поверхность металлической формы распылителем, щеткой, валиком или кистью. При необходимости смазку допускается нагревать до температуры 80°С. Оптимальный расход смазки составляет 30-35 г/м2 . По результатам токсикологической экспертизы смазка "Бетол-01" является малоопасным веществом и по степени воздействия на организм человека (согласно ГОСТ 12.1.007) отнесена к 4 классу опасности.
обеспечивать освобождение изделий из форм без повреждений;
не допускать загрязнения поддона и бортов формы остатками бетона;
не вызывать коррозии металлических форм;
быть недефицитной и несложной по технологии изготовления и нанесения;
быть безопасной в пожарном отношении;
быть однородной по составу и консистенции в процессе хранения;
хорошо удерживаться на вертикальных поверхностях форм;
образовывать сплошную пленку возможно меньшей толщины;
иметь низкую растворимость в воде, не проникать в поверхностный слой бетона и не оставлять жировых пятен;
быть безвредной для человека;
обладать устойчивостью при многократной оборачиваемости форм;
не высыхать и не терять качества в течение установленного времени.
Правильно выбранная смазка облегчает распалубку изделий и способствует получению ровной поверхности массивов без масляных пятен. Для смазки форм используют смеси составов со следующими массовыми соотношениями: петролатум – керосин 1:2,5; солидол / автол – керосин 1:1; кулисное и машинное масло 1:3; эмульсолы и др. В 2006 г. в Институте природопользования НАН Беларуси совместно с ОАО "Завод горного воска" разработана и внедрена в производство смазка "Бетол-01". В качестве основы смазки используют высоковязкие минеральные и растительные масла. Для обеспечения эксплуатационных свойств смазки в ее состав вводят комплекс антиадгезионных, вытесняющих, моющих и защитных присадок. Наличие в смазке маслорастворимых ПАВ позволяет создать на горизонтальных и вертикальных поверхностях опалубки прочный разделительный слой, обладающий высокими антиадгезионными свойствами (относительная величина снижения адгезии бетона к стали составляет не менее 97%). В состав смазки также введен маслорастворимый ингибитор коррозии на основе остаточного продукта крекинга масляных фракций. Форму, покрытую смазкой, можно длительное время хранить на открытом воздухе без потери ее потребительских свойств. По показателям кинематической вязкости при 40°С смазка "Бетол-01" соответствует диапазону 90-110 сСт (марка А) и 110-150 сСт (марка Б). Высокие эксплуатационные свойства смазки "Бетол-01" продлевают срок службы опалубки, защищая ее от коррозии. По комплексу эксплуатационных характеристик смазка "Бетол-01" не уступает немецкой смазке Addinol F150, однако существенно дешевле. Смазку наносят на внутреннюю поверхность металлической формы распылителем, щеткой, валиком или кистью. При необходимости смазку допускается нагревать до температуры 80°С. Оптимальный расход смазки составляет 30-35 г/м2 . По результатам токсикологической экспертизы смазка "Бетол-01" является малоопасным веществом и по степени воздействия на организм человека (согласно ГОСТ 12.1.007) отнесена к 4 классу опасности.
Арматура
Для изготовления арматуры (каркасов и сеток) применяют арматурную сталь, удовлетворяющую требованиям ГОСТ 10922 (рис. 6., 7.). Контрольные испытания прочности стали проводят по ГОСТ 12004.
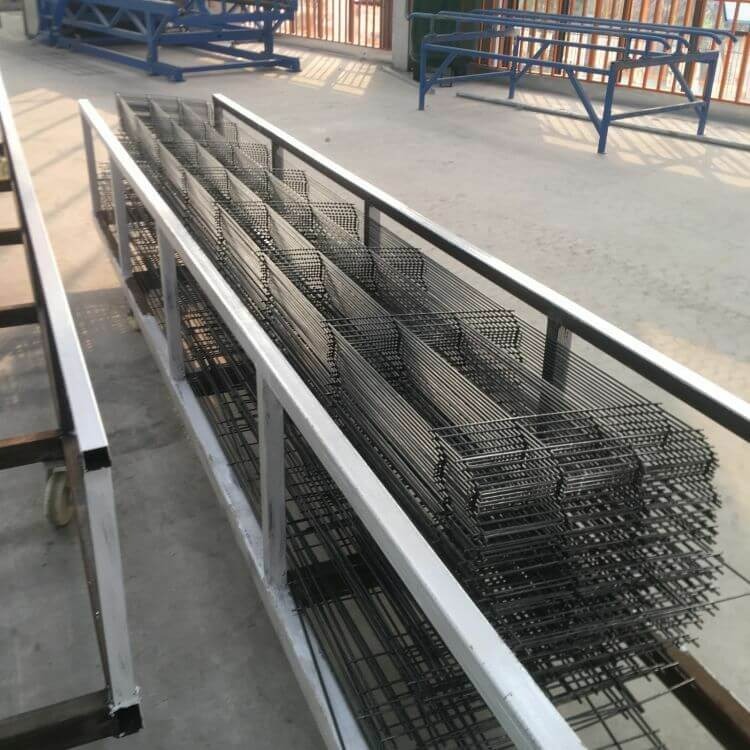
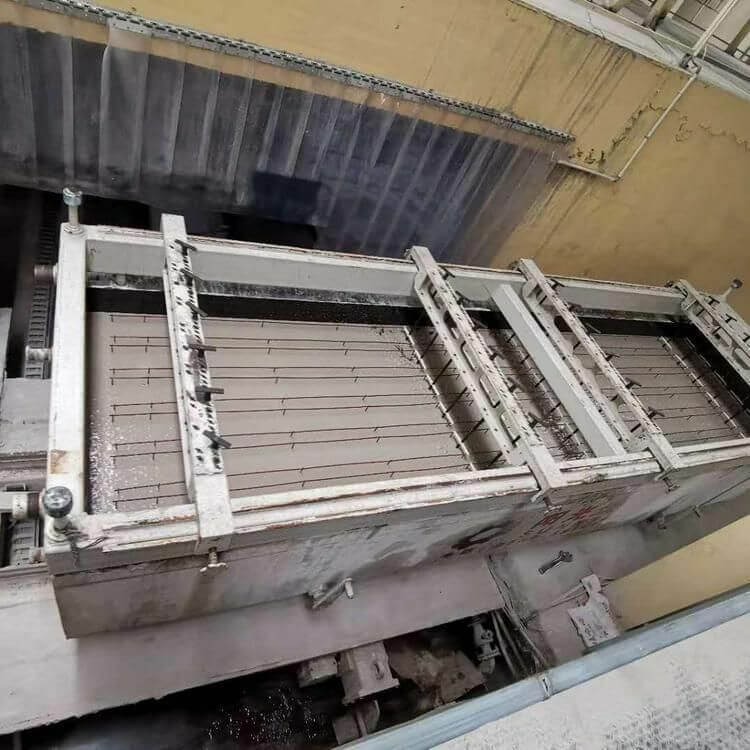
Арматурные каркасы и сетки в изделиях из ЯБ защищают антикоррозионными покрытиями. Поверхности каркасов и сеток перед нанесением покрытия должны быть сухими, без следов ржавчины и масла. В качестве антикоррозийного покрытия для арматуры используют мастику: холодную цементно-битумную; цементно-полистирольную; латексно-цементную; латексно-минеральную, ингибированную сланце-битумно-цементную; металлосиликатную и т.п. Антикоррозийные покрытия должны удовлетворять следующим требованиям: прочность на удар – не менее 1 МПа по ГОСТ 4765; эластичность не более 20 мм по ГОСТ 10086. Покрытие должно быть без трещин и сквозных пор и выдерживать транспортировку, штабелировку и укладку в форму без повреждений сплошности покрытия. Толщина слоя покрытия арматуры после сушки – 0,4-0,7 мм.
Мелющие тела
В качестве мелющих тел в мельницах мокрого помола используют шары из износостойкой, кованой и улучшенной стали с поверхностной твердостью 58-64 HRc и объемной твердостью 650-750 НВ, уменьшающейся от поверхности внутрь. Диаметр шаров подбирают в зависимости от характеристик песка, обычно 20/25/30/35 мм.
Проволока для агрегата резки
В качестве режущего инструмента используют проволоку пружинную стальную класса I по ГОСТ 9389 диаметром 0,6; 0,8 и 1,0 мм с прочностью при растяжении 2,3-2,6 ГПа.