Для изготовления ячеистого бетона используются композитные вяжущие, состоящие из цемента и извести. Отдельные предприятия могут работать на известково-белитовом, известково-шлаковом, зольном или шлакощелочном вяжущем. Подбор составов для этих вяжущих и технология изготовления изделий в каждом случае - отдельная задача, решаемая специалистами предприятий. Заводы автоклавного ячеистого бетона, работающие на цементе и извести, используют составы с различным соотношением цемент - известь. Под понятием «содержание извести» принято содержание активного СаО 100%. Для определения количества вводимой в состав извести производится перерасчет, учитывающий активность используемого вяжущего. Различают три типа композитного вяжущего. Первое - цементное. В цементном вяжущем преобладает цемент, а известь вводится в качестве добавки в количестве 10…20% от массы цемента. Второе -цементно-известковое, в котором отношение известь - цемент равно 1, с отклонением любого из компонентов до 25%. Третье - известковое, в котором преобладающим компонентом является известь, а цемент, в зависимости от требуемых свойств изделий, вводится в количестве от 20 до 50% от массы извести. Заводы неавтоклавного ячеистого бетона в качестве вяжущего используют цемент, иногда с добавкой до 10% извести. Добавка извести пластифицирует смесь и, в ряде случаев, облегчает работу предприятия по резательной технологии. Входящий в состав бетонов кремнеземистый компонент вводится в количестве, обеспечивающем требуемые показатели плотности бетона при выбранном типе вяжущего. При этом отношение кремнеземистого компонента к цементу и извести должно находиться в пределах, приводимых в таблице 1.

Большинство исследователей, изучавших ячеистый бетон, основной задачей считали получение изделий
максимальной прочности и решали вопросы технологии в отрыве от требуемых строительно-технических свойств изделий. Классическим примером этого является применение перегородок из ячеистого бетона. Исходя из требований по звукоизоляции, межкомнатные перегородки при толщине 100 мм должны иметь плотность 800 кг/м³. При этом прочность изделий более 50 кг/см² не требуется. Ячеистый бетон автоклавного твердения таких характеристик можно получить при расходе вяжущего ниже, чем рекоммендуемые расходы вяжущих в СН277-80. Водотвердое отношение Вт, принимают, исходя из технологии производства и температуры смеси. Для литьевой технологии Вт, принимают обычно в пределах от 0,45 до 0,6, в зависимости от требуемой плотности бетона и соотношения цемент - песок, при этом увеличение количества извести требует увеличения Вт. Контроль за правильностью подбора состава и Вт можно вести по показателю расплыва смеси, приведенному в таблице 2.
максимальной прочности и решали вопросы технологии в отрыве от требуемых строительно-технических свойств изделий. Классическим примером этого является применение перегородок из ячеистого бетона. Исходя из требований по звукоизоляции, межкомнатные перегородки при толщине 100 мм должны иметь плотность 800 кг/м³. При этом прочность изделий более 50 кг/см² не требуется. Ячеистый бетон автоклавного твердения таких характеристик можно получить при расходе вяжущего ниже, чем рекоммендуемые расходы вяжущих в СН277-80. Водотвердое отношение Вт, принимают, исходя из технологии производства и температуры смеси. Для литьевой технологии Вт, принимают обычно в пределах от 0,45 до 0,6, в зависимости от требуемой плотности бетона и соотношения цемент - песок, при этом увеличение количества извести требует увеличения Вт. Контроль за правильностью подбора состава и Вт можно вести по показателю расплыва смеси, приведенному в таблице 2.
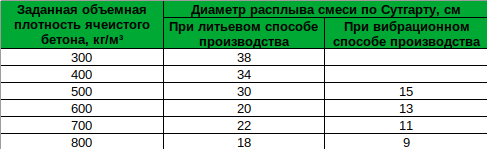
Температура смеси в момент её загрузки в форму должна составлять 40…45°С. После заливки смеси в форму ее температура начинает повышаться за счет выделения тепла от гидратации цементных минералов и извести. Реакция гидратации извести приводит к выделению 65.3 кДж на один моль материала Са + H2O=Ca(OH)2+65,3 кДж (15,64 ккал), или на 1кг извести выделяется 211,4 ккал. Для производства ячеистого бетона рекомендуется использовать известь со сроком гашения 8-20 минут. Это означает, что все тепло от гидратации извести выделяется на этапе от приготовления смеси до выдержки массива. Клинкерные минералы, входящие в состав цемента также выделяют тепло при гидратации, при этом количество тепла от гидратации цемента, в зависимости от состава клинкера, может составлять от 60 до 100 ккал на килограмм. Теплота гидратации основных клинкерных минералов составляет, в ккал/кг: для C3S - 136, для C3S - 62, для C4AF - 30, для C3A - 200. Гидратация цемента происходит гораздо медленнее, чем извести, и за первые трое суток выделяется до половины тепла гидратации. Учитывая, что температура смеси при заливке составляет 40 45°С, а скорость гидратации при повышении температуры на 10°С возрастает в два раза, до половины тепла гидратации цемента выделяется на
участке выдержки изделий до автоклавной обработки. Разогрев массы вследствие гидратации минералов, входящих в состав смеси, бывает особенно высоким при низком водотвердом отношении и при использовании известкового вяжущего. Смесь в форме при этом может разогреться до 85…95%. При быстром разогреве массы интенсифицируется процесс газообразования, в результате чего может произойти нарушение структуры бетона. Нарушения структуры бетона, происходящие при нахождении массы в форме, являются одной из причин снижения конечной прочности изделий, поскольку возникающие дефекты структуры полностью не залечиваются при выдержке и тепловой обработке. При изготовлении изделий из пенобетона температура смеси не должна превышать 30…35°С. Ориентировочные составы ячеистого бетона, для различных типов вяжущих и плотности бетона, приведены в таблице 3.
участке выдержки изделий до автоклавной обработки. Разогрев массы вследствие гидратации минералов, входящих в состав смеси, бывает особенно высоким при низком водотвердом отношении и при использовании известкового вяжущего. Смесь в форме при этом может разогреться до 85…95%. При быстром разогреве массы интенсифицируется процесс газообразования, в результате чего может произойти нарушение структуры бетона. Нарушения структуры бетона, происходящие при нахождении массы в форме, являются одной из причин снижения конечной прочности изделий, поскольку возникающие дефекты структуры полностью не залечиваются при выдержке и тепловой обработке. При изготовлении изделий из пенобетона температура смеси не должна превышать 30…35°С. Ориентировочные составы ячеистого бетона, для различных типов вяжущих и плотности бетона, приведены в таблице 3.
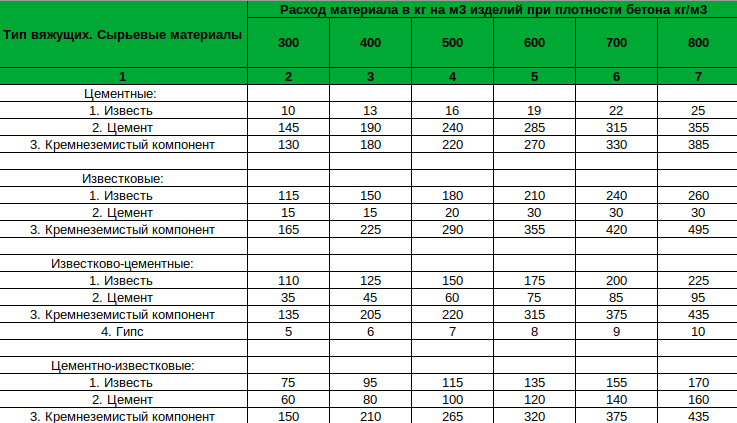
При производстве газобетона в качестве порообразующего компонента вводят алюминиевую пудру. Алюминиевая пудра взаимодействует с гидроокисью кальция с выделением водорода. Во время реакции из 1 кг алюминия выделяется 1,245 м³ водорода, а с учетом температуры смеси, равной 40°С, количество выделяемого водорода составит 1,425 м³/кг. В вяжущем на основе цемента реакция с выделением водорода происходит между алюминием и гидроокисью извести, образующейся при гидратации цемента. Для ускорения реакции выделения водорода в такое вяжущее иногда добавляют щелочь. Для интенсификации процесса газовыделения, температуру смеси при заливке ее в форму поддерживают на уровне 35…40°С. Часть водорода, выделяющегося в материале, уходит из массива и не участвует в процессе поризации бетона. Гидростатическое давление возрастает к нижней части массива, уменьшая физический объем пузырьков выделяющегося водорода, поэтому, рассчитывая количество алюминиевой пудры, принимают коэффициент использования выделяющегося водорода равным - 0,7…0,75. Количество алюминиевой пудры, добавляемой в смесь, в зависимости от плотности бетона и водотвердого отношения, приведено в таблице 4.
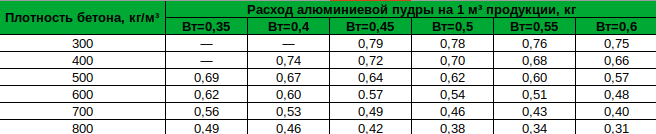
Приводимые цифры расхода алюминиевой пудры являются ориентировочными и должны уточняться при производстве. При производстве пенобетона количество пены, вводимой в раствор, определяется, исходя из необходимой плотности раствора. При этом коэффициент использования вводимой пены принимают от 0,7 до 0,8. Пенобетон приготавливают в смесителе, получая раствор требуемой плотности из всех компонентов смеси. В зависимости от В/т плотность раствора до введения пены может колебаться от 1,75 до 2 кг/литр. Плотность раствора Ар, после введения пены должна составлять:
Ар = (Ас + Ав • 0,1) • (1 + В/т);
где: (Ас + Ав • 0,1) = Аб - плотность формуемого пенобетона;
Ас - масса сухих компонентов в смеси;
Ав - масса вяжущих материалов в смеси;
В/т - водотвердое отношение.
Зная плотность пены, можно определить, сколько надо ее ввести для получения бетона требуемой плотности.
Количество вводимой пены можно ориентировочно найти из соотношения:
Ар = (Ас + Ав • 0,1) • (1 + В/т);
где: (Ас + Ав • 0,1) = Аб - плотность формуемого пенобетона;
Ас - масса сухих компонентов в смеси;
Ав - масса вяжущих материалов в смеси;
В/т - водотвердое отношение.
Зная плотность пены, можно определить, сколько надо ее ввести для получения бетона требуемой плотности.
Количество вводимой пены можно ориентировочно найти из соотношения:
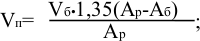
где: Vп- объем вводимой пены;
Vб - объем поризуемого бетона;
1,35 - коэффициент, учитывающий использование пены и увеличение объема бетона от воды, содержащейся в пене.
В процессе приготовления пенобетона целесообразно постоянно производить контроль плотности бетона и готовую смесь заливать в форму при достижении бетоном заданной плотности.
Vб - объем поризуемого бетона;
1,35 - коэффициент, учитывающий использование пены и увеличение объема бетона от воды, содержащейся в пене.
В процессе приготовления пенобетона целесообразно постоянно производить контроль плотности бетона и готовую смесь заливать в форму при достижении бетоном заданной плотности.
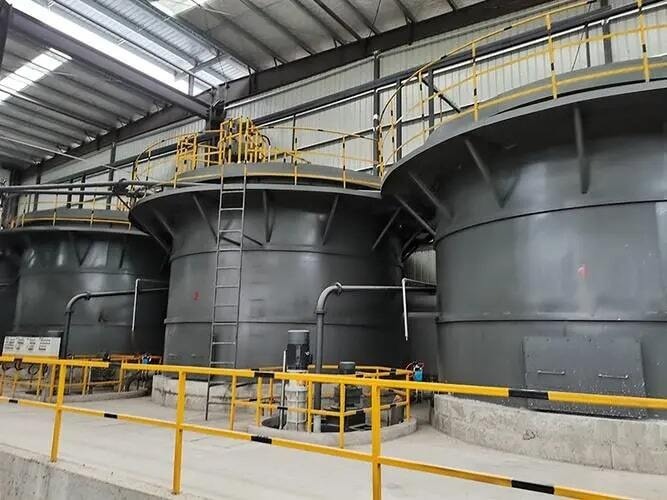