Характеризуя сырьевые материалы, предназначенные для производства ячеистого бетона, следует иметь в виду, что свойства исходных материалов и их подготовка существенно влияют на качество получаемых изделий.
Известь
В современной технологии ячеистых бетонов автоклавного твердения используют молотую негашеную известь, отвечающую требованиям ГОСТ 9179-77, Для производства ячеистого бетона наиболее пригодна известь, имеющая скорость гашения 10…18 минут и экзотермию 70-90°С.
На реакционную способность извести существенное влияние оказывает температура обжига и примесей, содержащихся в обжигаемом сырье.
Увеличение температуры обжига выше 1000…1200°С и времени пребывания извести при этой температуре вызывает перекристаллизацию окиси кальция с образованием пережога. Отличием пережженной извести является наличие кристаллов СaО размером от 50 до 100 микрон вместо кристаллов размером 1…3 микрона, характерных для кристаллов нормально обожженной извести. Кроме того, в извести обожженной при повышенной температуре могут содержаться клинкерные минералы (алит, алюмоферит), образующиеся при взаимодействии окиси кальция с минеральными примесями, содержащимися в сырье и имеющими другие свойства. Зависимость размеров кристаллов окиси кальция от температуры обжига представлена на рисунке 3.
На реакционную способность извести существенное влияние оказывает температура обжига и примесей, содержащихся в обжигаемом сырье.
Увеличение температуры обжига выше 1000…1200°С и времени пребывания извести при этой температуре вызывает перекристаллизацию окиси кальция с образованием пережога. Отличием пережженной извести является наличие кристаллов СaО размером от 50 до 100 микрон вместо кристаллов размером 1…3 микрона, характерных для кристаллов нормально обожженной извести. Кроме того, в извести обожженной при повышенной температуре могут содержаться клинкерные минералы (алит, алюмоферит), образующиеся при взаимодействии окиси кальция с минеральными примесями, содержащимися в сырье и имеющими другие свойства. Зависимость размеров кристаллов окиси кальция от температуры обжига представлена на рисунке 3.
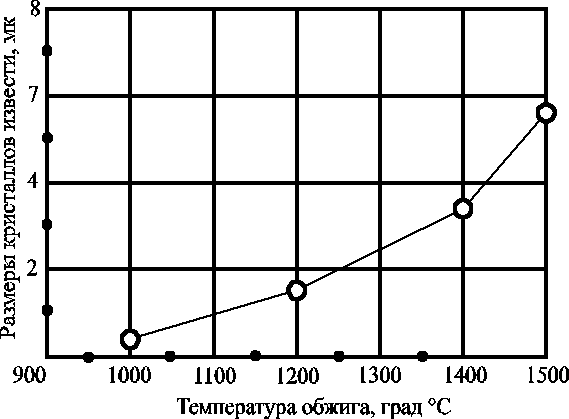
Высокая скорость гашения, 1-2 минуты, характерна для извести с размерами кристаллов до 1 мк. Увеличение размеров кристаллов до 2-4 мк приводит к замедлению скорости гидратации до 10-15 минут. Такая скорость гидратации наиболее отвечает требованиям технологии ячеистых бетонов. Пережженная известь, имеющая кристаллы в 50 и более микрон, может прогидратировать с изменением объема после формирования структуры бетона, что приводит к нарушению структуры изделий. Похожая картина наблюдается при наличии в извести окиси магния, имеющей значительно меньшую скорость гидратация, чем-то напоминающая кальцию. Поэтому количество пережога и окиси магния в составе извести для производства ячеистого бетона ограничивается в разных рекомендациях величиной от 3 до 5%.
Существенное влияние на скорость гидратации играет температура смеси. При повышении температуры на 10°С скорость гидратации увеличивается в два раза.
Скорость гашения можно регулировать введением в смесь добавок. Радулектролитов, пример NaCl, CaCl, и др., незначительно отличающийся от других Ca(ОН)2 и скорость гидратации, в то же время высокомолекулярные вещества замедляют ее растворимость. На заводах, работающих на быстрогасящейся извести, иногда используют технические лигносульфанты или триэтаноламин для замедления скорости гашения извести. С увеличением количества воды затворения, размер кристаллов Са(ОН)2 уменьшается, а с повышением температуры увеличивается. Из добавок, замедляющих гидратацию извести, в практике широко используется добавка двуводного гипса, который при введении его в состав бетона в количестве 3-5% от массы сухих компонентов замедляет скорость гидратации и увеличивает пластичность смеси.
Наличие в составе извести необожженного известняка приводит к образованию в материале при автоклавной обработке двойных солей кальция низкой прочности, которые могут привести к снижению прочности бетона. Для получения ячеистого бетона высокой прочности при плотности 400…500 кг/м³ желательно использовать известь активностью 85…95%.
Существенное влияние на скорость гидратации играет температура смеси. При повышении температуры на 10°С скорость гидратации увеличивается в два раза.
Скорость гашения можно регулировать введением в смесь добавок. Радулектролитов, пример NaCl, CaCl, и др., незначительно отличающийся от других Ca(ОН)2 и скорость гидратации, в то же время высокомолекулярные вещества замедляют ее растворимость. На заводах, работающих на быстрогасящейся извести, иногда используют технические лигносульфанты или триэтаноламин для замедления скорости гашения извести. С увеличением количества воды затворения, размер кристаллов Са(ОН)2 уменьшается, а с повышением температуры увеличивается. Из добавок, замедляющих гидратацию извести, в практике широко используется добавка двуводного гипса, который при введении его в состав бетона в количестве 3-5% от массы сухих компонентов замедляет скорость гидратации и увеличивает пластичность смеси.
Наличие в составе извести необожженного известняка приводит к образованию в материале при автоклавной обработке двойных солей кальция низкой прочности, которые могут привести к снижению прочности бетона. Для получения ячеистого бетона высокой прочности при плотности 400…500 кг/м³ желательно использовать известь активностью 85…95%.
Цемент
Известно, что при введении цемента в силикатный бетон в количестве 50…70 кг/м³ значительно улучшаются технологические свойства смеси, улучшается водоудерживающая способность массы, ускоряются процессы гидратации в автоклаве. Высокая степень гидратации цемента при автоклавной обработке приводит к повышенной прочности изделий. В технологии автоклавного ячеистого бетона рекомендуется использование бездобавочного цемента. Гидравлические добавки, включаемые в состав цемента, могут активно реагировать с известью, снижая тем самым количество образующихся гидросиликатов кальция и прочность изделий, поэтому добавки трепелов, глиежа, трасов, глинита, опоки и пеплов должны быть исключены. Содержание трехкальциевого алюмината в цементе по массе не более 8%. Наиболее эффективно использование в составе бетона клинкерного цемента M500D0.
Песок
Важную роль в формировании свойств ячеистого бетона имеет песок. Кварц, содержащийся в песке, более активен, чем полевой шпат, и активнее участвует в реакциях с окисью кальция. Содержащиеся в песке окислы щелочных металлов натрия и калия могут вызвать реакции с известью, приводящие к появлению трещин и разрушению изделий.
Поэтому содержание Na2O + K2O не должно превышать в песке 2%. Содержание илистых и глинистых материалов в песке, по разным источникам, не должно превышать 3-5%, содержание монтмориллонита -- 1,5-2 %.
Большую роль в реакциях образования новых соединений играет растворимость кварца. Растворимость кварца низкая и повышается с ростом температуры. При комнатной температуре растворимость кварца практически отсутствует. В щелочной среде растворимость кварца повышается и достигает максимума при температуре 150°С и концентрации СаО в растворе 0,033 г/литр.
Увеличение тонкости помола кварцевого песка ускоряет его растворение, повышает концентрацию раствора и интенсифицирует образование гидросиликатов. В зависимости от концентрации Ca(OH)2 и SiO2 в растворе могут образовываться гидросиликаты разной основности.
Поэтому количество и дисперстность кварца и извести имеют большое значение в технологии ячеистого бетона. Для получения ячеистого бетона высокого качества необходимо использовать песок с содержанием кристаллического кварца не менее 85%.
Поэтому содержание Na2O + K2O не должно превышать в песке 2%. Содержание илистых и глинистых материалов в песке, по разным источникам, не должно превышать 3-5%, содержание монтмориллонита -- 1,5-2 %.
Большую роль в реакциях образования новых соединений играет растворимость кварца. Растворимость кварца низкая и повышается с ростом температуры. При комнатной температуре растворимость кварца практически отсутствует. В щелочной среде растворимость кварца повышается и достигает максимума при температуре 150°С и концентрации СаО в растворе 0,033 г/литр.
Увеличение тонкости помола кварцевого песка ускоряет его растворение, повышает концентрацию раствора и интенсифицирует образование гидросиликатов. В зависимости от концентрации Ca(OH)2 и SiO2 в растворе могут образовываться гидросиликаты разной основности.
Поэтому количество и дисперстность кварца и извести имеют большое значение в технологии ячеистого бетона. Для получения ячеистого бетона высокого качества необходимо использовать песок с содержанием кристаллического кварца не менее 85%.
Гипс
В технологии ячеистого бетона широко используется двуводный гипс, который вводят в количестве 10…30 кг/м3 изделий. Вместо двуводного гипса на некоторых заводах Европы и других стран используется природный ангидрит - безводный гипс.
Добавка гипса регулирует скорость гидратации извести, воздействуя тем самым на изменение температуры смеси и процесс газообразования. В дальнейшем гипс оказывает модифицирующее влияние на образование гидросиликатов и приводит к улучшению качества бетона.
Гипс применяют тонкомолотый с удельной поверхностью не менее 3000 см2/г. Содержание минерала CaSO3x3(H2O) в гипсовом камне должно быть не менее 85%.
Добавка гипса регулирует скорость гидратации извести, воздействуя тем самым на изменение температуры смеси и процесс газообразования. В дальнейшем гипс оказывает модифицирующее влияние на образование гидросиликатов и приводит к улучшению качества бетона.
Гипс применяют тонкомолотый с удельной поверхностью не менее 3000 см2/г. Содержание минерала CaSO3x3(H2O) в гипсовом камне должно быть не менее 85%.
Порообразующие добавки
Пористую структуру в ячеистых бетонах получают, вводя в состав смеси или газообразователь, или техническую пену. В качестве газообразователя используют алюминиевую пудру, получаемую помолом алюминия, с последующей парафинизацией порошка. Алюминиевая пудра, используемая в качестве газообразователя на большинстве заводов РФ, поставляется российскими заводами и отвечает требованиям ГОСТ5494-95. В технологии ячеистого бетона применяется алюминиевая пудра марок ПАП-1 и ПАП-2.
ПАП-1 имеет кроющую способность 7000 см2/г, ПАП-2 - 10 000 см2/г. Большинство заводов использует пудру ПАП-1. Пудра представляет собой лепестки толщиной 0,3…0,5 мк, размером 20…30 мк. Лепестки для предотвращения окисления алюминия имеют пленочное покрытие из парафина или органических масел в количестве 38 г на 1 кг алюминия. Содержание металлического алюминия в материале не менее 95%. Иногда алюминиевый порошок поставляется в виде пасты.
Алюминиевая пудра относится к пожаро- и взрывоопасным веществам группы А и должна храниться в соответствии с требованиями СНиП II-90-81. Хранение пудры должно производиться при температуре не выше 35С, на расстоянии не ближе 1 метра от приборов отопления. При использовании пудры в качестве газообразователя из одного килограмма металлического алюминия при температуре 40°C выделяется ~1,42м3 водорода.
Часть выделяемого водорода попадает в атмосферу. Условия вентиляции и объемы здания таковы, что пожароопасной концентрации водорода в помещении не может образоваться и категорийность участка приготовления и дозирования алюминиевой пудры не выделяется из общей категории здания. Для исключения взаимодействия алюминия с воздухом пудра поставляется в герметических металлических банках.
В зависимости от условий поставки для пудры и пасты используются разные схемы подготовки алюминиевой пудры для введения ее в смесь.
ПАП-1 имеет кроющую способность 7000 см2/г, ПАП-2 - 10 000 см2/г. Большинство заводов использует пудру ПАП-1. Пудра представляет собой лепестки толщиной 0,3…0,5 мк, размером 20…30 мк. Лепестки для предотвращения окисления алюминия имеют пленочное покрытие из парафина или органических масел в количестве 38 г на 1 кг алюминия. Содержание металлического алюминия в материале не менее 95%. Иногда алюминиевый порошок поставляется в виде пасты.
Алюминиевая пудра относится к пожаро- и взрывоопасным веществам группы А и должна храниться в соответствии с требованиями СНиП II-90-81. Хранение пудры должно производиться при температуре не выше 35С, на расстоянии не ближе 1 метра от приборов отопления. При использовании пудры в качестве газообразователя из одного килограмма металлического алюминия при температуре 40°C выделяется ~1,42м3 водорода.
Часть выделяемого водорода попадает в атмосферу. Условия вентиляции и объемы здания таковы, что пожароопасной концентрации водорода в помещении не может образоваться и категорийность участка приготовления и дозирования алюминиевой пудры не выделяется из общей категории здания. Для исключения взаимодействия алюминия с воздухом пудра поставляется в герметических металлических банках.
В зависимости от условий поставки для пудры и пасты используются разные схемы подготовки алюминиевой пудры для введения ее в смесь.
Пенообразователи
Для получения пористой структуры бетона за счет введения технической пены используются, в основном, высокомолекулярные синтетические пенообразователи различного химического состава. Поставка пенообразователей осуществляется в виде концентрированного раствора основного вещества. Для получения из концентрата пены необходимо развести его водой до определенной концентрации, обеспечивающей максимальную его эффективность. У пенообразователей эта концентрация различна, и следует использовать величины, рекомендуемые в паспорте данного пенообразователя или получить у производителя.
Практически все пенообразователи наиболее эффективны при определенной температуре, как правило, 30…35°С. Для большинства пенообразователей повышение температуры до 40…45°С приводит к разрушению структуры пены, поэтому до завершения процесса схватывания смеси повышать температуру выше 40°С не рекомендуется. Одной из особенностей пенообразователей
является замедление скорости гидратации цемента при их введении. Замедление скорости гидратации цемента при использовании пенообразователей приводит к увеличению времени выдержки массивов до разрезки и может привести к разной прочности изделий из неавтоклавного ячеистого бетона, одинаковой плотности и состава, при использовании различных пенообразователей. Наилучшие показатели получаются при использовании пенообразователей на основе модифицированного протеина. На территории РФ наибольшее распространение получили пенообразователь ПБ-2000, разработанный специально для пенобетона, и пожарные пенообразователи типа ПО6, ПО10А и различные модификации на их основе. Работа пенообразователей существенно зависит от химического состава цемента и вводимых в него добавок, поэтому при работе с использованием пенообразователей нежелательно менять поставщика цемента.
Практически все пенообразователи наиболее эффективны при определенной температуре, как правило, 30…35°С. Для большинства пенообразователей повышение температуры до 40…45°С приводит к разрушению структуры пены, поэтому до завершения процесса схватывания смеси повышать температуру выше 40°С не рекомендуется. Одной из особенностей пенообразователей
является замедление скорости гидратации цемента при их введении. Замедление скорости гидратации цемента при использовании пенообразователей приводит к увеличению времени выдержки массивов до разрезки и может привести к разной прочности изделий из неавтоклавного ячеистого бетона, одинаковой плотности и состава, при использовании различных пенообразователей. Наилучшие показатели получаются при использовании пенообразователей на основе модифицированного протеина. На территории РФ наибольшее распространение получили пенообразователь ПБ-2000, разработанный специально для пенобетона, и пожарные пенообразователи типа ПО6, ПО10А и различные модификации на их основе. Работа пенообразователей существенно зависит от химического состава цемента и вводимых в него добавок, поэтому при работе с использованием пенообразователей нежелательно менять поставщика цемента.